paulcook
Mechanical
- Oct 2, 2023
- 46
Designing a cast aluminum part (ADC12 alloy), and trying to determine an adequate distance from the center of the tapped hole to the edge of the material.
Bolt is 5/16-18 stainless + loctite.
Depth > 3X bolt diameter.
For distance from the threaded hole center to the edge, we have about0.77" 0.85":
Is using the diameter of the circumscribing circle of a standard (aluminum) nut not a reasonable approach to finding the minimum?
I am confused on the standard 1.5 - 2D rule of thumb. Is that from the center of the hole, or the edge?
Have also seen 3X thread height as a rule of thumb, but that seems like much less than >1.5D.
Bolt is 5/16-18 stainless + loctite.
Depth > 3X bolt diameter.
For distance from the threaded hole center to the edge, we have about
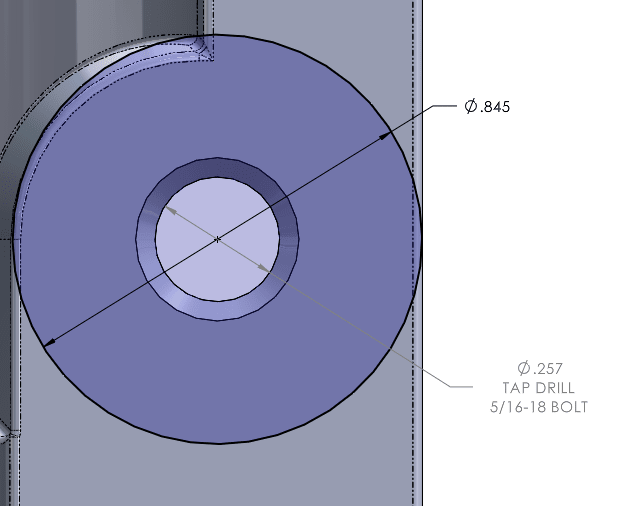
Is using the diameter of the circumscribing circle of a standard (aluminum) nut not a reasonable approach to finding the minimum?
I am confused on the standard 1.5 - 2D rule of thumb. Is that from the center of the hole, or the edge?
Have also seen 3X thread height as a rule of thumb, but that seems like much less than >1.5D.