Good day to everyone.
I am working on repair of a 50 v DC torque motor. It is used within a digital feedback control system for precise positioning of an arm. The angular position is given by a synchro resolver to control system. The rotor's winding was burnt and a new rotor was needed since the winding was fully concealed in potting epoxy.
The winding scheme / wire gauge of motor’s rotor was reverse engineered by me from original rotor. I used two parallel coils of # 33 gauge wire between commutator segments, as in original rotor. The core of the rotor was made using wire erosion / cut process on a stack of 0.5mm electrical sheet. After soldering the coils with commutator segments, the winding was potted using electrical epoxy and brought to final diameter size by grinding process. Kapton sheet was used as insulation in slots / between commutator segments. Photographs of winding diagram, rotor core, permanent magnet stator and finished rotor are shown for reference.
The developed rotor has performed well and gives similar RPM (200-300 rpm at full voltage) but there are two problems. The starting voltage of repaired motor (with new rotor) is higher now as compared with original rotor. The starting current is also higher. The original motor started moving at less than 1.0 vdc at 0.1 Amp current, whereas the repaired motor starts at approx 7.0 vdc with higher current of 0.25 – 0.5 amps. Secondly, the repaired motor has less torque than original motor. No other items in the motor were changed in addition to developed rotor (i.e carbon brushes, permanent magnet stator, bearings / covers / fittings etc).
Pl advice what can be done to achieve a smaller starting voltage and better torque.
I am working on repair of a 50 v DC torque motor. It is used within a digital feedback control system for precise positioning of an arm. The angular position is given by a synchro resolver to control system. The rotor's winding was burnt and a new rotor was needed since the winding was fully concealed in potting epoxy.
The winding scheme / wire gauge of motor’s rotor was reverse engineered by me from original rotor. I used two parallel coils of # 33 gauge wire between commutator segments, as in original rotor. The core of the rotor was made using wire erosion / cut process on a stack of 0.5mm electrical sheet. After soldering the coils with commutator segments, the winding was potted using electrical epoxy and brought to final diameter size by grinding process. Kapton sheet was used as insulation in slots / between commutator segments. Photographs of winding diagram, rotor core, permanent magnet stator and finished rotor are shown for reference.
The developed rotor has performed well and gives similar RPM (200-300 rpm at full voltage) but there are two problems. The starting voltage of repaired motor (with new rotor) is higher now as compared with original rotor. The starting current is also higher. The original motor started moving at less than 1.0 vdc at 0.1 Amp current, whereas the repaired motor starts at approx 7.0 vdc with higher current of 0.25 – 0.5 amps. Secondly, the repaired motor has less torque than original motor. No other items in the motor were changed in addition to developed rotor (i.e carbon brushes, permanent magnet stator, bearings / covers / fittings etc).
Pl advice what can be done to achieve a smaller starting voltage and better torque.
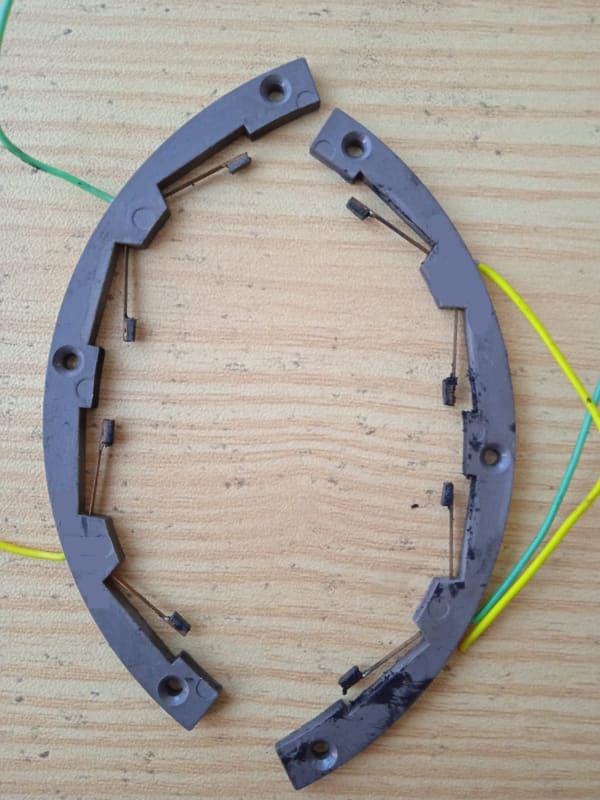
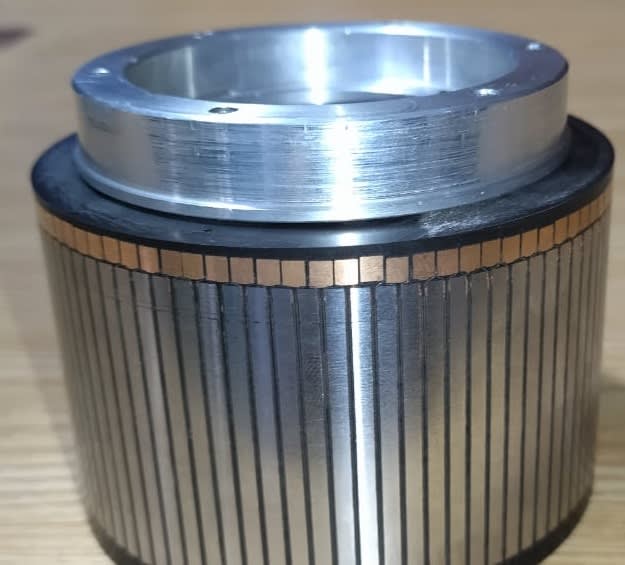
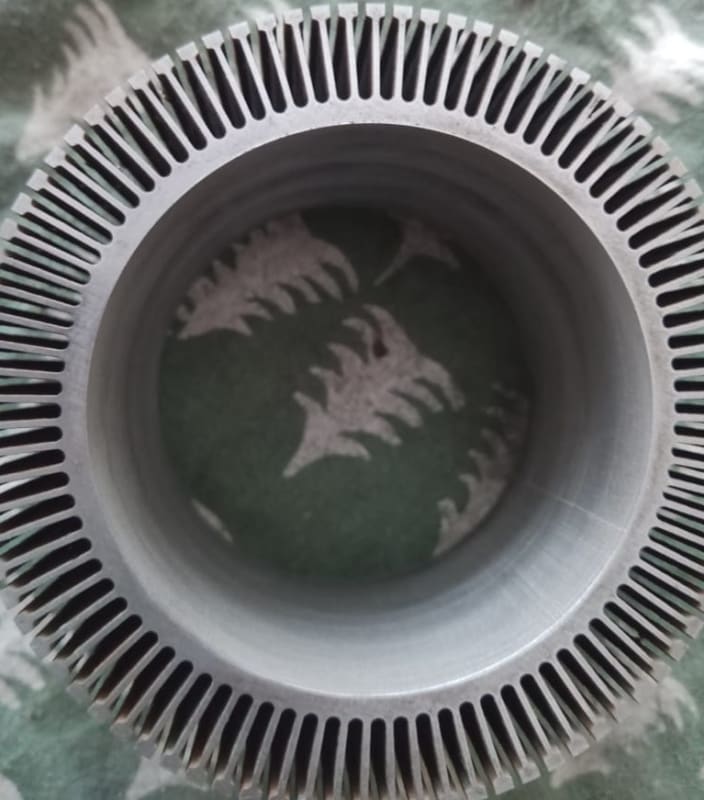
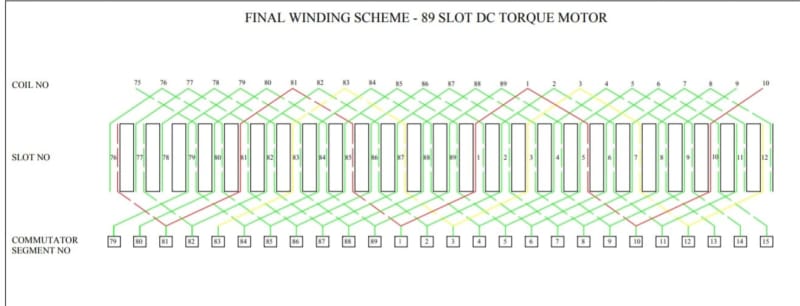
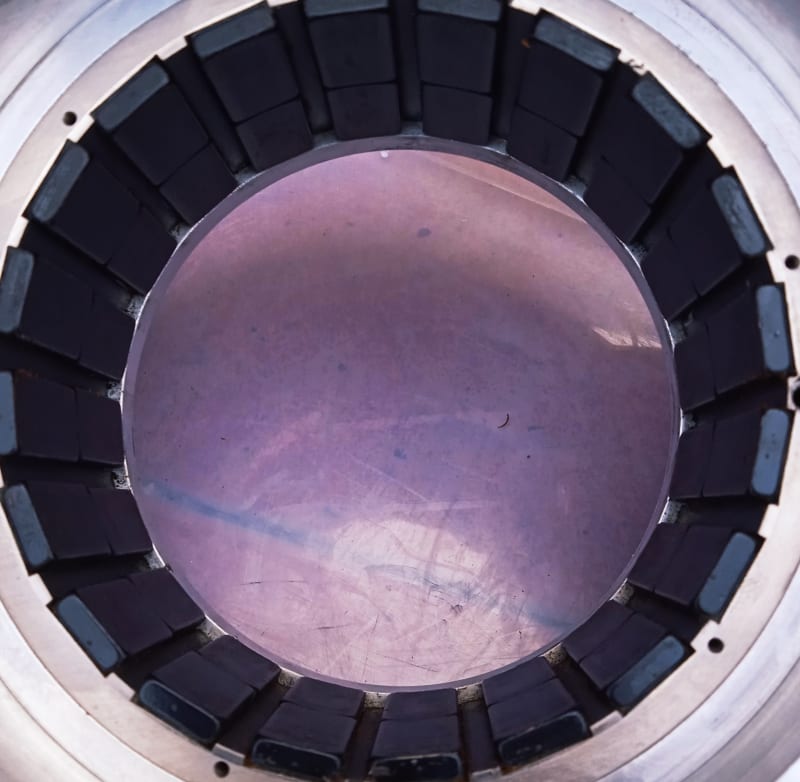