hirschaplin
Petroleum
- Jul 10, 2021
- 60
Hello,
I am working for a compressor manufacturer. For the last couple of projects delivering various gas compression systems I have been struggling to find the ultimate lifting facility (lugs, padeye etc.) for transportation and installation of our skids.
The best engineering just looks right, that perfect harmony between different elements creating confidence in the design. Yet it must be simple and easy to manufacture with as little engineering work as possible.
What is the best, most simple and elegant solution to lift a skid designed by H/I beams and other standard steel construction products.
Few criterias
- Safe and reliable usage for max. 5 lifts in the life time of the design
- Cost effective
- Simple design made with standard steel construction products - welded/bolted together
- Sometimes the lifting facility can be permanetly attached to the skid but sometimes the customer require that it can be removed after finalization
- Easy to understand the integrity and limits of the lifting facility - for example, it should not be necessary to run complicated calculations to understand how strong the design is - what rule of thumb can be used?
- How to attach the lifting facility to the H/I beam? How to reinforce the beam in the best, most simple way?
- Total overall weight between 2.000 and 50.000 kg divided by 4 lifting facilities.
- Material S355 steel grades
- Scalable for various sizes of beams, i.e. HEB 180 and HEB 400 in order to have consistency in our design between projects
Some example of previous lifting facilities, we are basically trying something new in each of the last projects... I don't like it. I want our design to be consistent.
Type 1
Type 2
Type 3
Type 4
Type 5
Type 6
Type 7
Type 8
Typically how our skids are lifted:
With your help I am hoping to find the best design that we thereafter can standardize for different lifting weights and beam sizes.
Thank you in advance.
I am working for a compressor manufacturer. For the last couple of projects delivering various gas compression systems I have been struggling to find the ultimate lifting facility (lugs, padeye etc.) for transportation and installation of our skids.
The best engineering just looks right, that perfect harmony between different elements creating confidence in the design. Yet it must be simple and easy to manufacture with as little engineering work as possible.
What is the best, most simple and elegant solution to lift a skid designed by H/I beams and other standard steel construction products.
Few criterias
- Safe and reliable usage for max. 5 lifts in the life time of the design
- Cost effective
- Simple design made with standard steel construction products - welded/bolted together
- Sometimes the lifting facility can be permanetly attached to the skid but sometimes the customer require that it can be removed after finalization
- Easy to understand the integrity and limits of the lifting facility - for example, it should not be necessary to run complicated calculations to understand how strong the design is - what rule of thumb can be used?
- How to attach the lifting facility to the H/I beam? How to reinforce the beam in the best, most simple way?
- Total overall weight between 2.000 and 50.000 kg divided by 4 lifting facilities.
- Material S355 steel grades
- Scalable for various sizes of beams, i.e. HEB 180 and HEB 400 in order to have consistency in our design between projects
Some example of previous lifting facilities, we are basically trying something new in each of the last projects... I don't like it. I want our design to be consistent.
Type 1

Type 2
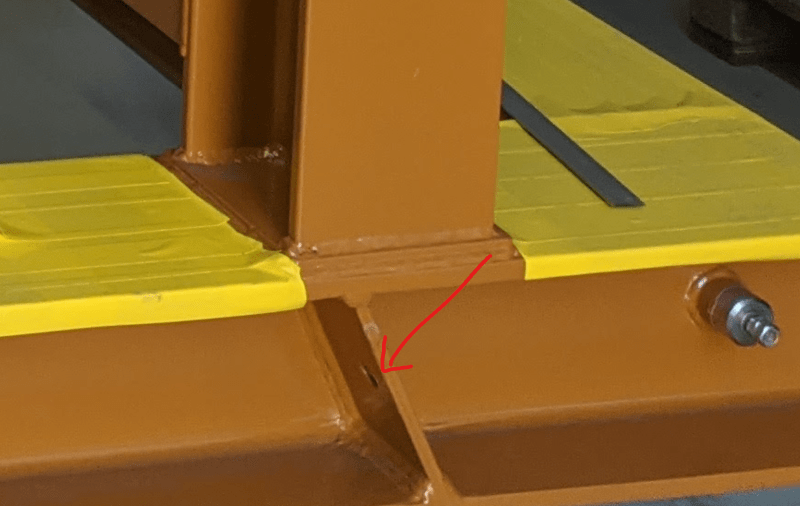
Type 3
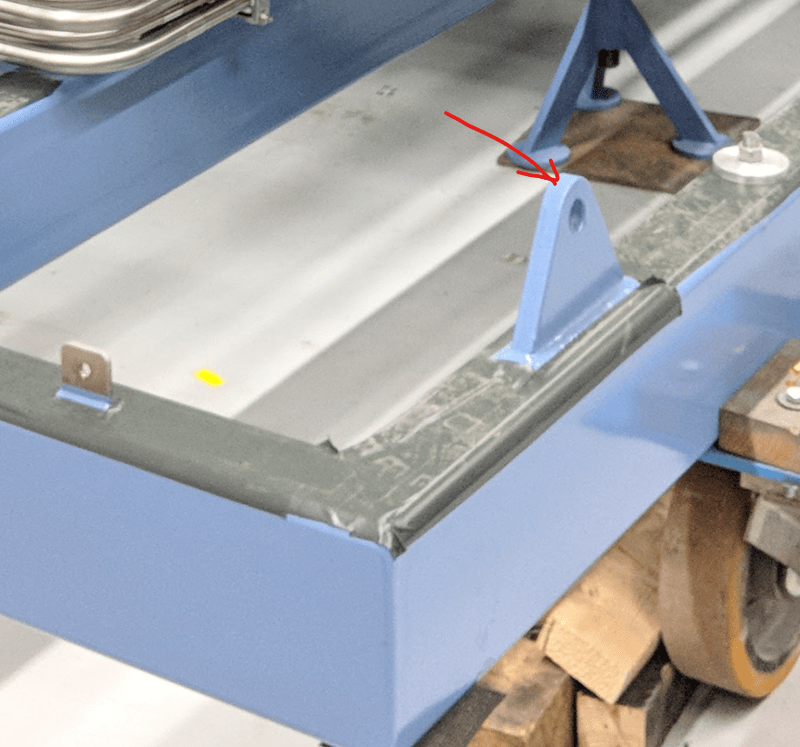
Type 4
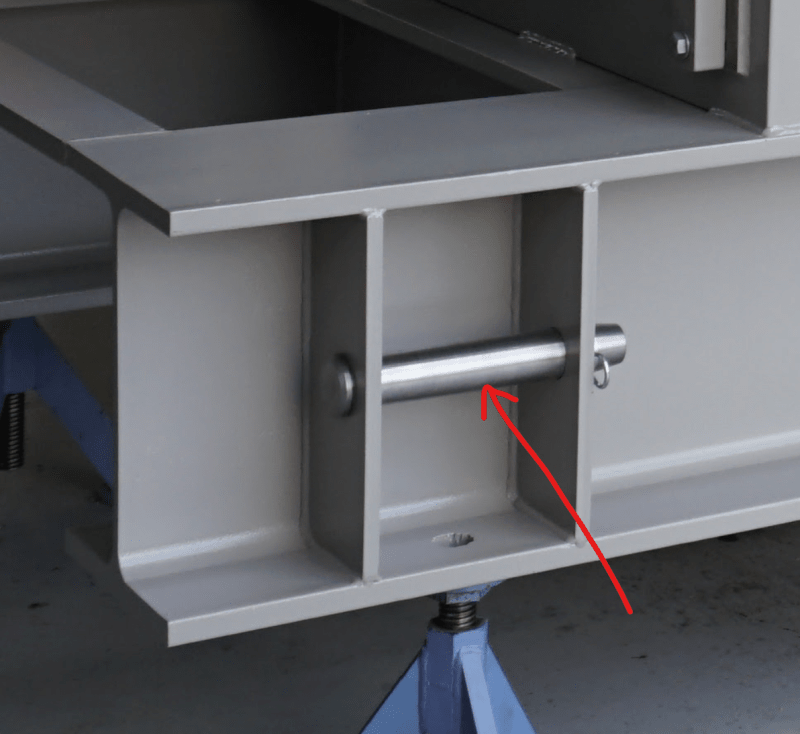
Type 5

Type 6
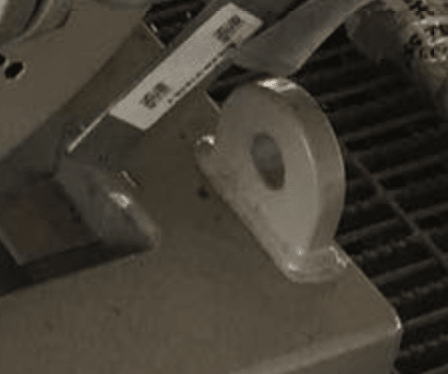
Type 7
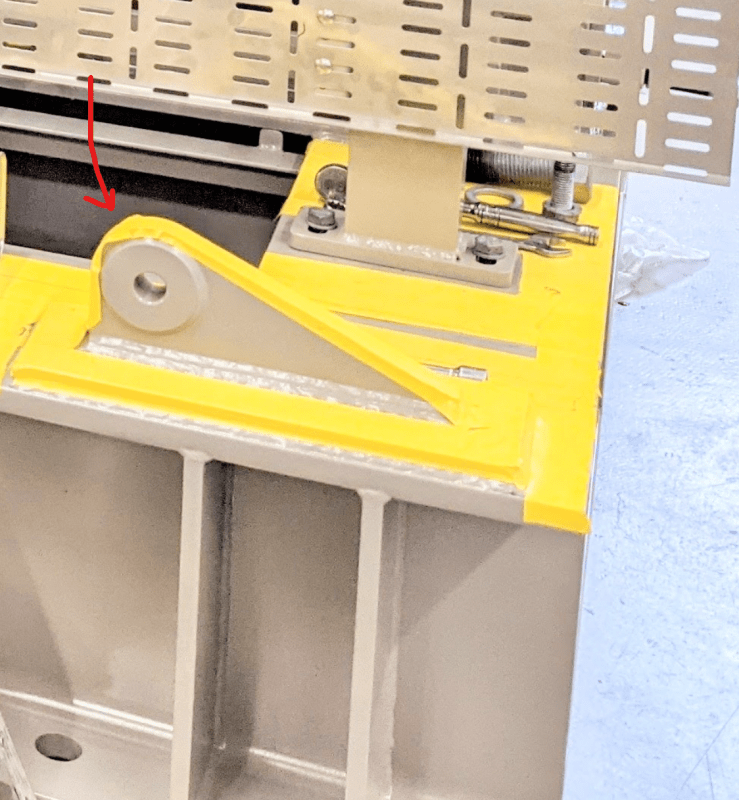
Type 8
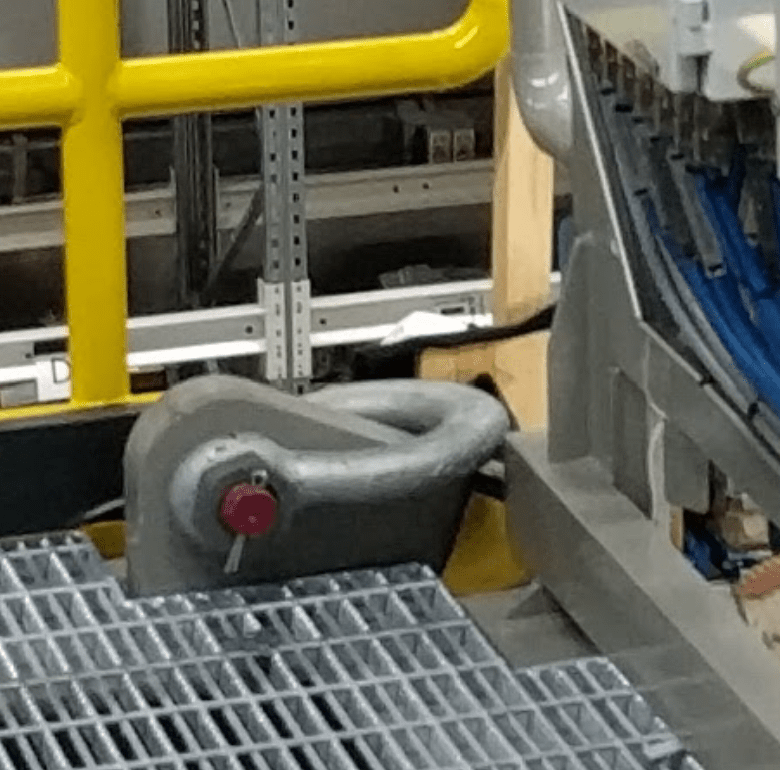
Typically how our skids are lifted:
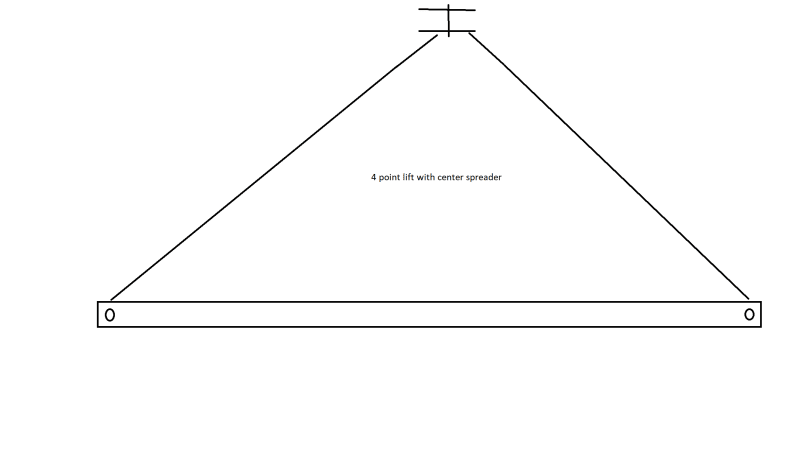
With your help I am hoping to find the best design that we thereafter can standardize for different lifting weights and beam sizes.
Thank you in advance.