Amir35
Mechanical
- Jun 7, 2016
- 20
Dear Gentlemen
Here we have a problem ,we are going to weld a 19 mm carbon steel flange hub, with 3 mm inconel 625 overlay ,to a 14 mm Solid inconel pipe, Executing team has presented a plan to build up the pipe with 8 mm inconel and then start welding. On the other hand, we have no free space for using transition piece.
ASME B31.3 Code book recommends using transition piece for this case{Fig 328.3.2(a)}but we have no more room, Then mentioned procedure is not supported by ASME B31.3 Code book,
There are 90 joints like this on each deck and pipe service is sour gas and I don’t feel good about thickness build up .
I appreciate if you let me know your opinion.
Regards
Amir Rokhsativand
Piping Engineer
Here we have a problem ,we are going to weld a 19 mm carbon steel flange hub, with 3 mm inconel 625 overlay ,to a 14 mm Solid inconel pipe, Executing team has presented a plan to build up the pipe with 8 mm inconel and then start welding. On the other hand, we have no free space for using transition piece.
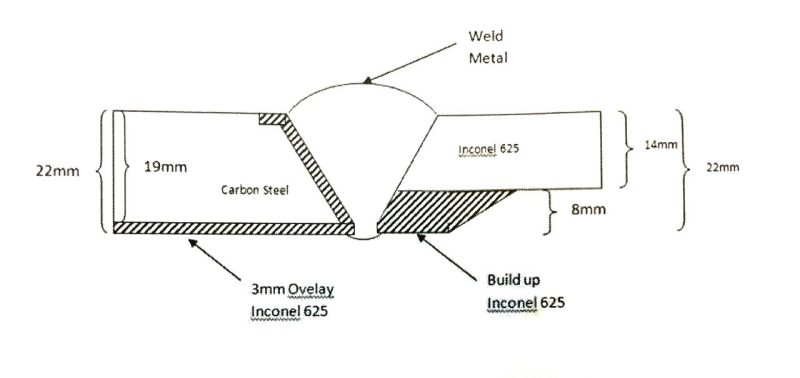
ASME B31.3 Code book recommends using transition piece for this case{Fig 328.3.2(a)}but we have no more room, Then mentioned procedure is not supported by ASME B31.3 Code book,
There are 90 joints like this on each deck and pipe service is sour gas and I don’t feel good about thickness build up .
I appreciate if you let me know your opinion.
Regards
Amir Rokhsativand
Piping Engineer