Hello,
I would like to explore what options do I have in replacing steel (welded plate + ribs) cover with something much lighter, machinable, stiff and shape stable. Price does not play an important role.
Current welded piece is apprx: 30 x 20 inches, with 0.03" thick base plate, ribs are 0,15 x 0.15"
As mentioned: at approx. 0.8 kg this part is somehow heavy. It is stiff enough not to bend too much when manually handled. I would like to know, if there any options in plastic/carbon range of material, that would allow us to reproduce part with similar mechanical characteristics and yet benefit in weight reduction.
Thanks for all answers in advance.
I would like to explore what options do I have in replacing steel (welded plate + ribs) cover with something much lighter, machinable, stiff and shape stable. Price does not play an important role.
Current welded piece is apprx: 30 x 20 inches, with 0.03" thick base plate, ribs are 0,15 x 0.15"
As mentioned: at approx. 0.8 kg this part is somehow heavy. It is stiff enough not to bend too much when manually handled. I would like to know, if there any options in plastic/carbon range of material, that would allow us to reproduce part with similar mechanical characteristics and yet benefit in weight reduction.
Thanks for all answers in advance.
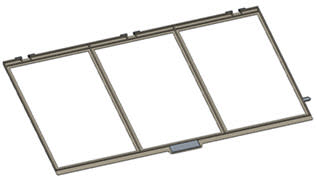