ThinCap
Mechanical
- Oct 17, 2019
- 34
We recently had a tube end burst incident. The pressure is from outside of this tube:
The end broke and shot out from the middle of the tube. We usually test it with pressure from inside since when the thickness is uniform, there probably not much difference from either in or outside. And we never had any failure when tested from inside.
But when the end is so thin, quarter thickness of the tube wall, the yield mode/stress will still be the same? I can't find any theoretical solutions for this case. Did any of you had similar situation and analysis before? What is your conclusion? Thanks!
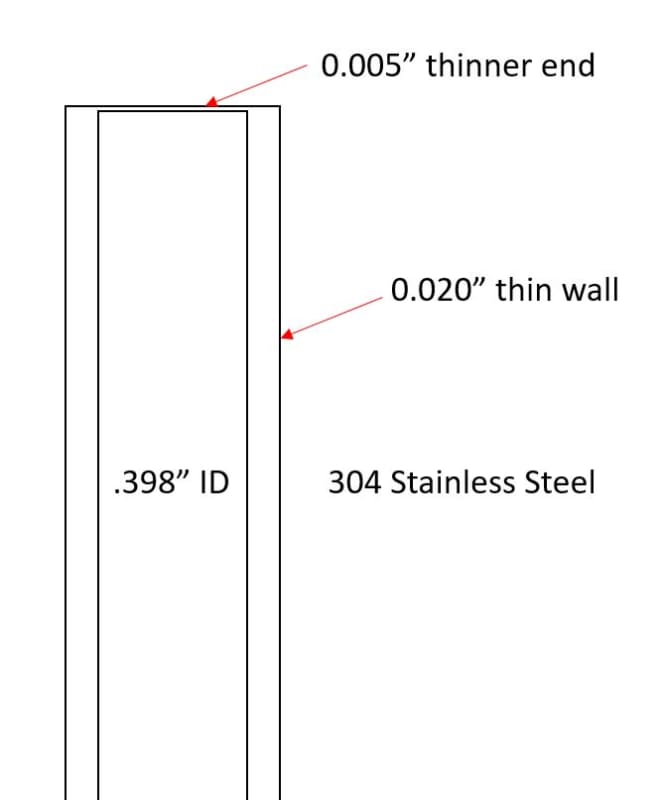
The end broke and shot out from the middle of the tube. We usually test it with pressure from inside since when the thickness is uniform, there probably not much difference from either in or outside. And we never had any failure when tested from inside.
But when the end is so thin, quarter thickness of the tube wall, the yield mode/stress will still be the same? I can't find any theoretical solutions for this case. Did any of you had similar situation and analysis before? What is your conclusion? Thanks!