BoxOhJelly
Materials
- Feb 26, 2025
- 5
Hello forum, interested to hear what thoughts y'all may have about this really weird looking corrosion I found.
Parts are thin wall 304L stainless tubing, annealed. They get filled with good ole tap water but failures are very random, sometimes they'll last a few days, sometimes a few months or even a few years. Some don't fail at all.
I've seen a good number of failures so far, but I have only seen this phenomenon once before back in October and now again this week so here I am asking about it.
First particular instance, it was filled for 3 hours before leak was discovered.
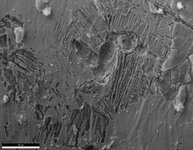
Second particular instance, only info I have is that it leaked 19 days after installation.
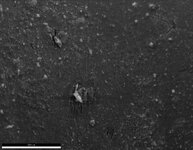
My first thought was preferential dissolution of cementite/ferrite in pearlite because of the lamellar kind of look to it but then I remembered this is austenitic. My other idea was slip bands or twinning, something along the lines of higher stressed regions, corrosion starts on areas with the highest energy, but I just dont think that's right (too small of a pattern to be twinning, and the tubes are not under any external stresses besides simply existing, and they're annealed so shouldn't be any residual stresses). The tubes can vary in length though these were both 72 inches long, different spots along the tube, not near the weld seam, not the same water between these two occurrences.
Appreciate any and all thoughts you peeps may have!
-BoJ
Parts are thin wall 304L stainless tubing, annealed. They get filled with good ole tap water but failures are very random, sometimes they'll last a few days, sometimes a few months or even a few years. Some don't fail at all.
I've seen a good number of failures so far, but I have only seen this phenomenon once before back in October and now again this week so here I am asking about it.
First particular instance, it was filled for 3 hours before leak was discovered.
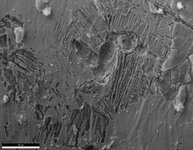
Second particular instance, only info I have is that it leaked 19 days after installation.
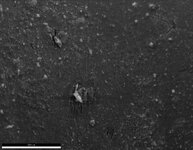
My first thought was preferential dissolution of cementite/ferrite in pearlite because of the lamellar kind of look to it but then I remembered this is austenitic. My other idea was slip bands or twinning, something along the lines of higher stressed regions, corrosion starts on areas with the highest energy, but I just dont think that's right (too small of a pattern to be twinning, and the tubes are not under any external stresses besides simply existing, and they're annealed so shouldn't be any residual stresses). The tubes can vary in length though these were both 72 inches long, different spots along the tube, not near the weld seam, not the same water between these two occurrences.
Appreciate any and all thoughts you peeps may have!
-BoJ