LoneStarEngineer
Structural
I have an elevated concrete platform modeled in RISA 3D and I am researching on performing a time history analysis for the structure. The equipment manufacturer has provided a set of dynamic loads at the rotor support points for both horizontal and vertical directions. I have assigned sine functions for vertical loads and cosine functions for horizontal loads. I have three machines, two running at the same frequency and the 3rd one running at a higher frequency. I also have cosine functions with 180 degree phase angle for a separate load case.
How does RISA handle load cases under a common time history tag? Should I define one time history tag with all the loads in X, Y and Z directions like below? I think keeping the load tags separate for each load direction would be more appropriate but wanted to get more opinions. Moreover, do I have to combine loads in horizontal and vertical directions within the same load tag?
Is there a good reference on which time history load directions need to be considered/combined together for a load case? Appreciate any inputs. Thanks.
How does RISA handle load cases under a common time history tag? Should I define one time history tag with all the loads in X, Y and Z directions like below? I think keeping the load tags separate for each load direction would be more appropriate but wanted to get more opinions. Moreover, do I have to combine loads in horizontal and vertical directions within the same load tag?
Is there a good reference on which time history load directions need to be considered/combined together for a load case? Appreciate any inputs. Thanks.
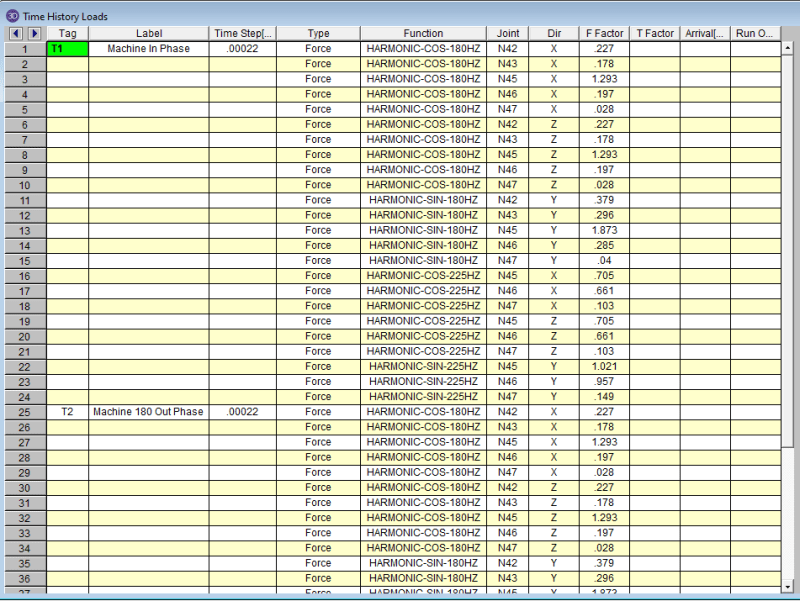