Garrett Green
Mechanical
I am being asked to approve something but I have no way to verify through calculations so I am hoping someone with more experience can tell me if this is a bad idea.
Essentially we have a timing shaft that we through drill and use a spring pin to attach a coupling. the through hole was drilled off center so they want to rotate the shaft 90° and drill a new hole so we can still use the shaft.
I have looked into stress concentration and I found Kfs to be 2.52 for the original hole, but I can not find a way to calculate the stress concentration for a second hole (probably because there is no reason to do it). Even if I could calculate this unfortunately I can not calculate life of the rod using any failure theories because the moment on the rod will depend on how much weight the customer puts on this along with how well it is built and how much friction it sees. My thinking is, if I could calculate the stress concentration added by drilling a second hole it would give me an idea how much it will weaken the shaft so I can make a more educated guess.
More parameters:
diameter of rod = 0.625"
rod material = 1018 CD Steel
Sut = 63800psi
hole diameter = 0.1875"
hole distance from the end of shaft = 0.5"
There should be no bending stress, it should be purely rotational. I can elaborate on why if you need to know.
This image should help:
If my idea for stress concentration seems like the right approach does anyone know how to calculate this? if not, does anyone have a better starting point for me?
Thank you!
Essentially we have a timing shaft that we through drill and use a spring pin to attach a coupling. the through hole was drilled off center so they want to rotate the shaft 90° and drill a new hole so we can still use the shaft.
I have looked into stress concentration and I found Kfs to be 2.52 for the original hole, but I can not find a way to calculate the stress concentration for a second hole (probably because there is no reason to do it). Even if I could calculate this unfortunately I can not calculate life of the rod using any failure theories because the moment on the rod will depend on how much weight the customer puts on this along with how well it is built and how much friction it sees. My thinking is, if I could calculate the stress concentration added by drilling a second hole it would give me an idea how much it will weaken the shaft so I can make a more educated guess.
More parameters:
diameter of rod = 0.625"
rod material = 1018 CD Steel
Sut = 63800psi
hole diameter = 0.1875"
hole distance from the end of shaft = 0.5"
There should be no bending stress, it should be purely rotational. I can elaborate on why if you need to know.
This image should help:
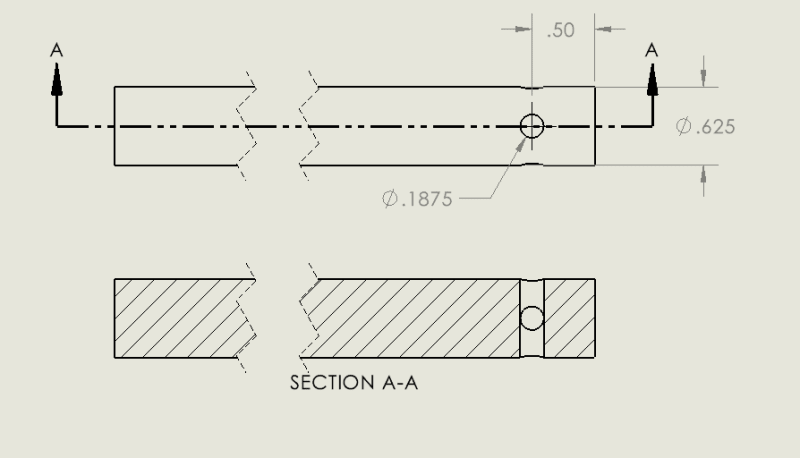
If my idea for stress concentration seems like the right approach does anyone know how to calculate this? if not, does anyone have a better starting point for me?
Thank you!