Hi all,
I have designed a 3 point bending test of a concrete beam and did topology optimization on it. Attached below is the result, I am generally satisfied with it but I have been trying to smoothen the sharp edges and introduce a symmetry about the middle (Left half design = Right half design) but can't seem to figure out how.
I thought of re-designing the problem as half the length and mirror the TO design afterwards. But am wondering if there is any geometric restriction that exist that I could use in Abaqus.
Would appreciate it if anyone could advice/help! Thank you in advance!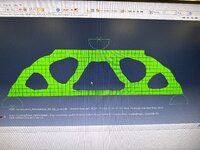
I have designed a 3 point bending test of a concrete beam and did topology optimization on it. Attached below is the result, I am generally satisfied with it but I have been trying to smoothen the sharp edges and introduce a symmetry about the middle (Left half design = Right half design) but can't seem to figure out how.
I thought of re-designing the problem as half the length and mirror the TO design afterwards. But am wondering if there is any geometric restriction that exist that I could use in Abaqus.
Would appreciate it if anyone could advice/help! Thank you in advance!
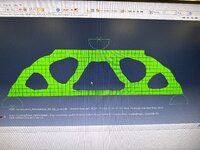