Hello, there is probably a simple answer to this, but i have not been able to find it.
I am familiar with the idea that the max available torque from a wheel is dependent on the static load radius, load on the wheel, and the friction between the wheel and ground.
I am tying to determine the load path of this torque to the wheel studs. In the example picture, there are 5 wheel studs.
I know the studs see vertical loading evenly. So with 5 studs, each stud sees a vertical load equal to “W/5”.
Would the torque be distributed evenly between these 5 wheel studs?
If a take the bolt circle of the wheel studs, would dividing the wheel torque by the bolt circle radius determine the shear force acting on the wheel stud?
Or does a strong clamp load prevent the studs from seeing any torque or shear loading, and the torque is simply distributed to the hub?
Thanks!
Mike
I am familiar with the idea that the max available torque from a wheel is dependent on the static load radius, load on the wheel, and the friction between the wheel and ground.
I am tying to determine the load path of this torque to the wheel studs. In the example picture, there are 5 wheel studs.
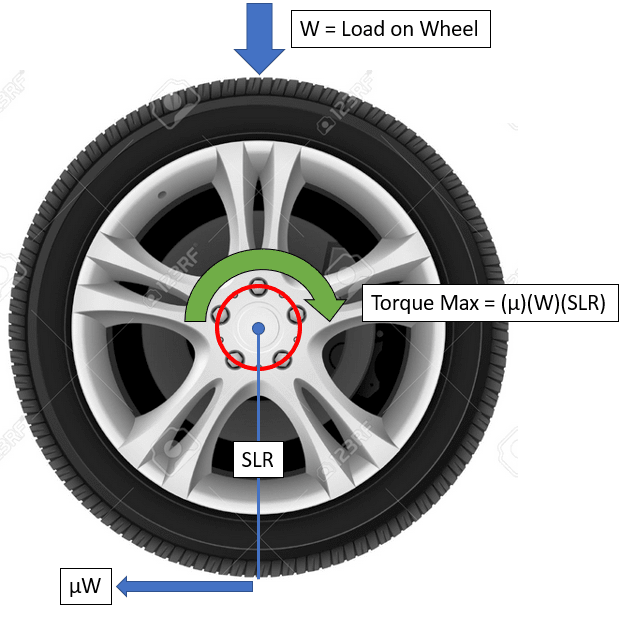
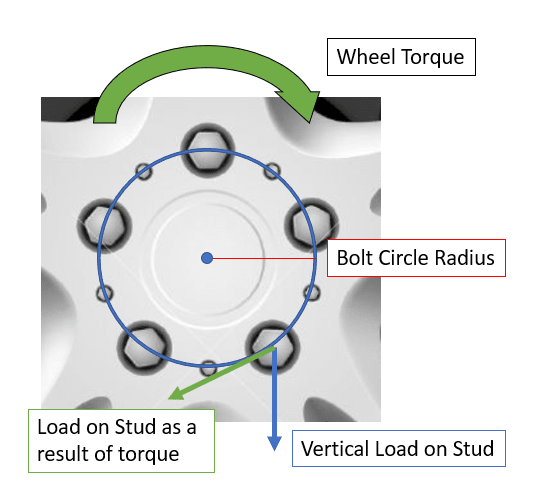
I know the studs see vertical loading evenly. So with 5 studs, each stud sees a vertical load equal to “W/5”.
Would the torque be distributed evenly between these 5 wheel studs?
If a take the bolt circle of the wheel studs, would dividing the wheel torque by the bolt circle radius determine the shear force acting on the wheel stud?
Or does a strong clamp load prevent the studs from seeing any torque or shear loading, and the torque is simply distributed to the hub?
Thanks!
Mike