Dear Forum Members,
I don't know if this is the right forum but I'm sure the gurus present would shed some light. We have a gearbox arrangement and the motor/gearbox assembly drives a shaft which itself drives a conveyor. The gearbox was removed for maintenance and now it has just been put into position. We are looking for the right procedure and the correct torque to tighten the shrink disc bolts on the gearbox. See the attached picture. We contacted the OEM but without much success. The gearbox is rated @ 3200 k Nm.
Thank you.
Guardiano
I don't know if this is the right forum but I'm sure the gurus present would shed some light. We have a gearbox arrangement and the motor/gearbox assembly drives a shaft which itself drives a conveyor. The gearbox was removed for maintenance and now it has just been put into position. We are looking for the right procedure and the correct torque to tighten the shrink disc bolts on the gearbox. See the attached picture. We contacted the OEM but without much success. The gearbox is rated @ 3200 k Nm.
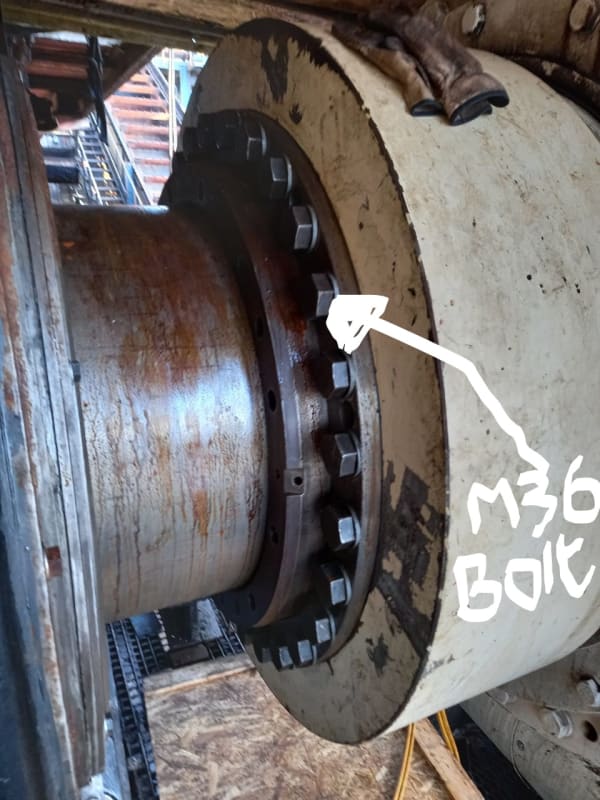
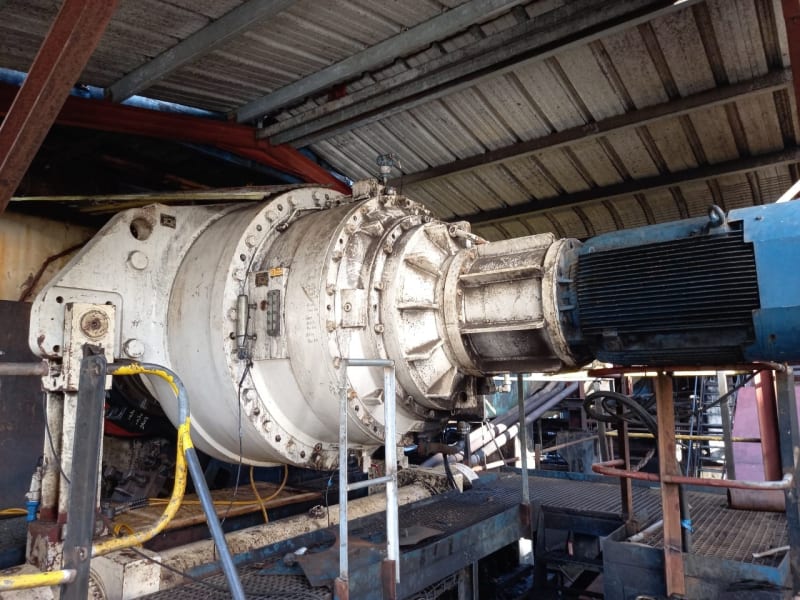
Thank you.
Guardiano