JustUseSteel
Structural
I have a precast, prestressed inverted tee beam with significant torsion. It needs to dap onto another beam to receive it. Does torsional reinforcing need to extend into the nib? I believe it should, however my senior has told me otherwise - the crack will form after the re-entrant corner, so stirrups "before" the bearing pad are not needed / would not engage.
I have not been able to figure out in my head whats happening, conceptually. Given the nib/ledge have a depth - say 6" - we must assume the bearing stresses are somewhat uniform over that 6" x nib width section. So torsional stresses would be maximum at the re-entrant corner, and fade over the bearing pad. But would that stress/crack engage a stirrup within the nib?
I have not been able to figure out in my head whats happening, conceptually. Given the nib/ledge have a depth - say 6" - we must assume the bearing stresses are somewhat uniform over that 6" x nib width section. So torsional stresses would be maximum at the re-entrant corner, and fade over the bearing pad. But would that stress/crack engage a stirrup within the nib?
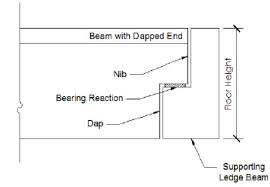