bangerjoe
Industrial
- Oct 16, 2013
- 35
hello
I have a lug on a beam loaded at a fleet angle.
this may be a very elementary question but am i ok to check for biaxial bending.
can't find any standards/examples that use torsion and biaxial bending.
Thanks for any help
I have a lug on a beam loaded at a fleet angle.
this may be a very elementary question but am i ok to check for biaxial bending.
can't find any standards/examples that use torsion and biaxial bending.
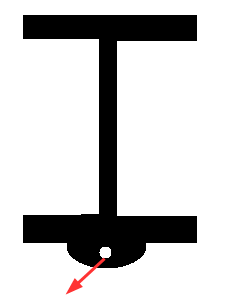
Thanks for any help