I am trying to solve for maximum shear stress on a notched round bar being driven by a direct drive motor giving torque T which is also machining something with a force F as shown below.
Max shear stress where Ip = polar moment of inertia of the cross section with respect to the center
R is radius
T is Torque
Text book examples seem to assume a fixed end when calculating shear stress... how can we calculate the torque increase when a force is applied in the opposite direction of the motor?
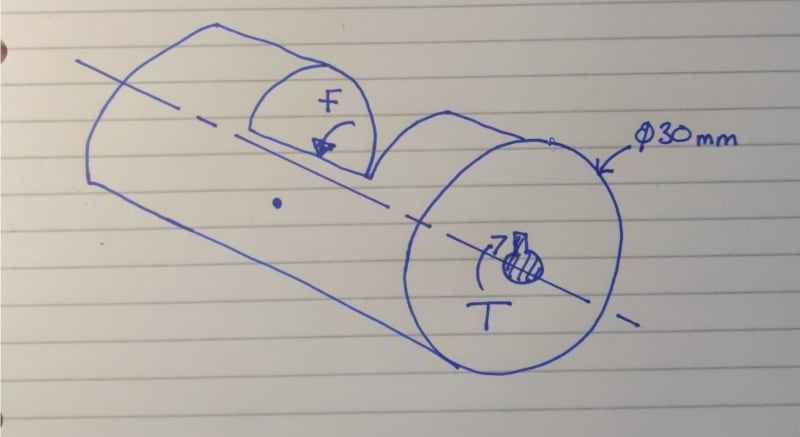
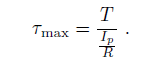
Max shear stress where Ip = polar moment of inertia of the cross section with respect to the center
R is radius
T is Torque
Text book examples seem to assume a fixed end when calculating shear stress... how can we calculate the torque increase when a force is applied in the opposite direction of the motor?