VPOW
Mechanical
- Feb 8, 2021
- 5
hi there,
I have attached two torsion spring image. My understanding, to get optimum spring force from the torsion spring, the angle between the spring arm is critical. I have spoken to spring a manufacture however not very helpful but i got confused. Apparent, it is not the long arm that determine the between the spring angle. Im totally confused. Any spring expert out there that can advise. Can anyone tell me what is the best way to determine the spring
arm?
I have attached two torsion spring image. My understanding, to get optimum spring force from the torsion spring, the angle between the spring arm is critical. I have spoken to spring a manufacture however not very helpful but i got confused. Apparent, it is not the long arm that determine the between the spring angle. Im totally confused. Any spring expert out there that can advise. Can anyone tell me what is the best way to determine the spring
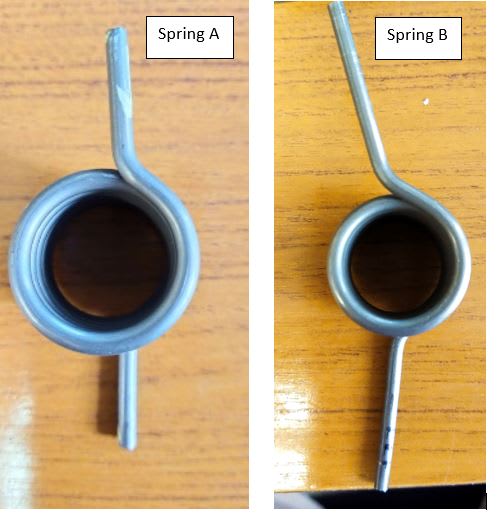