James Hornett
Structural
Hi,
My company is currently dealing with a difficult problem.
We recently reviewed a waste transfer station (built late 1990s). The station consists of a metal framed structure over a concrete foundation. There are two levels. At the upper level trash is dumped onto a slab-on-grade. The trash is loosely sorted and then pushed to a openings in the floor below where transport trailers are positioned to take the trash. At the openings the slab on grade transitions to a suspended slab. Due to the original slab becoming damaged, a few years after the building was constructed, a topping layer (approx. 6") was added to the slab. The drawings from that project indicate that additional rebar was added to help support the suspended slab.
Problem: moisture is visible at the underside of the suspended slab and corrosion of the rebar is beginning. Spalled concrete was not observed though. Although covered by the metal structure above, moisture from the trash and from equipment moving into and out of the building renders it effectively an outdoor space. During original construction and at the time of repairs it does not appear that a waterproof membrane was applied to protect the suspended slab. We have considered removing a portion of the topping, applying a membrane and adding a topping back over. The amount of concrete that needs to be removed would likely mean a significant shutdown which the client would like to avoid. We also looked at removing a small portion of concrete (approximately 3/4"), applying a membrane and installing metal panels over. Heavy equipment including equipment with tracks are used to move the trash. The client felt that there would not be enough grip with the steel plates.
We briefly looked at applying a robust traffic membrane directly to the concrete however we doubt it would last long given the nature of the work.
If anyone has seen a similar situation or knows of a possible solution, please let me know.
Thank you
My company is currently dealing with a difficult problem.
We recently reviewed a waste transfer station (built late 1990s). The station consists of a metal framed structure over a concrete foundation. There are two levels. At the upper level trash is dumped onto a slab-on-grade. The trash is loosely sorted and then pushed to a openings in the floor below where transport trailers are positioned to take the trash. At the openings the slab on grade transitions to a suspended slab. Due to the original slab becoming damaged, a few years after the building was constructed, a topping layer (approx. 6") was added to the slab. The drawings from that project indicate that additional rebar was added to help support the suspended slab.
Problem: moisture is visible at the underside of the suspended slab and corrosion of the rebar is beginning. Spalled concrete was not observed though. Although covered by the metal structure above, moisture from the trash and from equipment moving into and out of the building renders it effectively an outdoor space. During original construction and at the time of repairs it does not appear that a waterproof membrane was applied to protect the suspended slab. We have considered removing a portion of the topping, applying a membrane and adding a topping back over. The amount of concrete that needs to be removed would likely mean a significant shutdown which the client would like to avoid. We also looked at removing a small portion of concrete (approximately 3/4"), applying a membrane and installing metal panels over. Heavy equipment including equipment with tracks are used to move the trash. The client felt that there would not be enough grip with the steel plates.
We briefly looked at applying a robust traffic membrane directly to the concrete however we doubt it would last long given the nature of the work.
If anyone has seen a similar situation or knows of a possible solution, please let me know.
Thank you
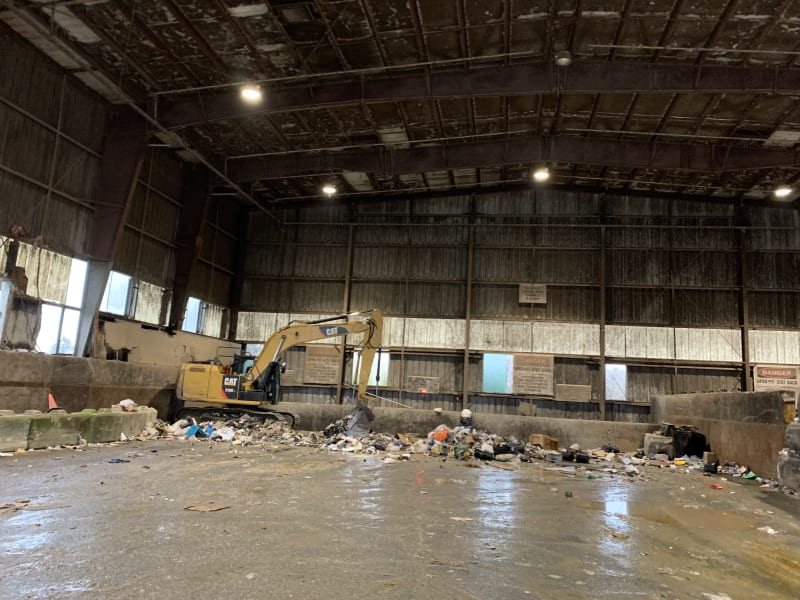