Hello, could someone please have a look at the true position callout on the left-hand view in the attached image and let me know if this makes any sense at all? I'm thinking not, as it's placement doesn't seem to indicate that it is associated with any feature of size. I'm thinking that profile of a surface is the correct callout for this surface.
I've found multiple other issues as well... The runout tolerance is total overkill on this part as that chamfer is only there to clear a radius in a molded plastic part it mates with. The surface I first mentioned really only needs to be perpendicular to datum feature C and have a relatively tight tolerance on the positional dimension to ensure interchangeability.
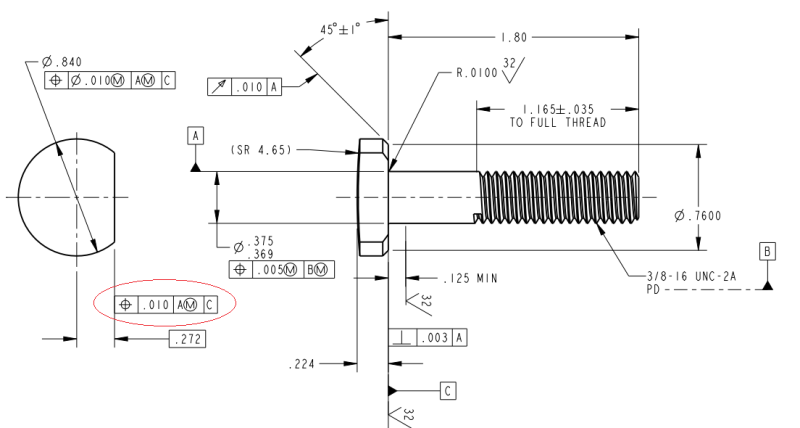
I've found multiple other issues as well... The runout tolerance is total overkill on this part as that chamfer is only there to clear a radius in a molded plastic part it mates with. The surface I first mentioned really only needs to be perpendicular to datum feature C and have a relatively tight tolerance on the positional dimension to ensure interchangeability.