BAGW
Structural
- Jul 15, 2015
- 392
Hi,
See image below. The diagonals are in compression and vertical is in tension. When I sum up all the components for the gusset to chord design, the forces adds up to be zero. This does not make sense. How do you come up with the forces for the gusset to chord design? I dont think splitting the plate into half and checking for the local forces is correct.
Any thoughts. Can I just design for 140k of vertical force?
Thanks
See image below. The diagonals are in compression and vertical is in tension. When I sum up all the components for the gusset to chord design, the forces adds up to be zero. This does not make sense. How do you come up with the forces for the gusset to chord design? I dont think splitting the plate into half and checking for the local forces is correct.
Any thoughts. Can I just design for 140k of vertical force?
Thanks
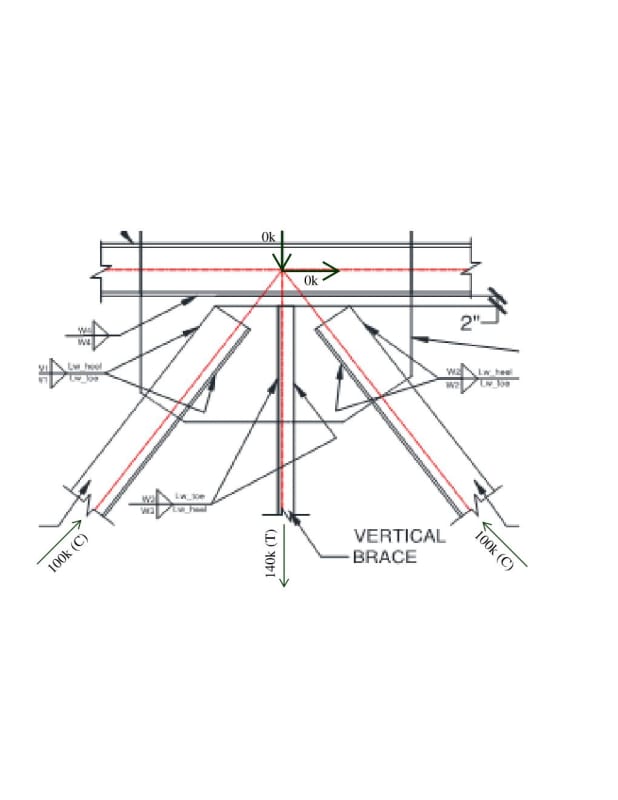