thread337-18639
I'm now about to embark on the wood gusset stage of my truss designer. I've been reading and searching the internet for as many resources as I can in relation to how to best fasten these plates to the truss members.
As a given I will probably spec. out a glue (ie. LNP-902) which I will not consider in the strength calculations to give an additional level of redundancy and margin to the design.
Looking through a number of documents I've seen clinched 3" nails, and unclinched 6d, 8d and 10d nails used. I've even seen some mention of Simpson SDS screws as well as drywall screws. Most of these documents are 50 years old or older so not a lot of recent data on this topic or so it would seem.
I am curious if anyone has any recent experience with using plywood or osb gusset plates on wood trusses and what was their fastener of choice and why?
I really like the idea of 3" nails that are clinched (less nails = less labor) however would a smaller diameter nail be less prone to splitting the wood members even though there are more of them and they are spaced more closely together?
I'm also considering ringshank nails since the cyclic loading on a truss might have a tendency to back the nails out over time, however the shear strength of these nails is a question needing further investigation.
For the actual gusset plate material I'm considering 1/2" DF Structural I Plywood, however I would also like to have 3/4" PLY, 19/32" PLY and 7/16" OSB as additional options. I've actually see 7/16" OSB used in a lot of home built trusses and I'm actually guilty myself of my own home brewed trusses for a small storage shed using drywall screws and 7/16" OSB (8 ft. span). Other than the strength design values are there any other caveats to using OSB in this application?
A confused student is a good student.
Nathaniel P. Wilkerson, PE
I'm now about to embark on the wood gusset stage of my truss designer. I've been reading and searching the internet for as many resources as I can in relation to how to best fasten these plates to the truss members.
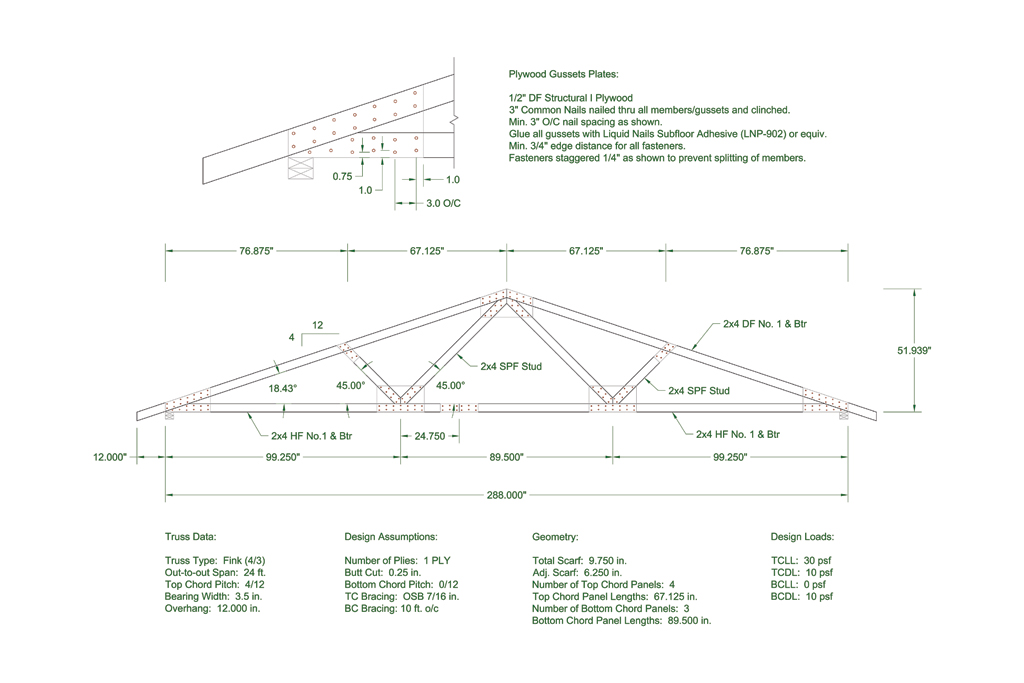
As a given I will probably spec. out a glue (ie. LNP-902) which I will not consider in the strength calculations to give an additional level of redundancy and margin to the design.
Looking through a number of documents I've seen clinched 3" nails, and unclinched 6d, 8d and 10d nails used. I've even seen some mention of Simpson SDS screws as well as drywall screws. Most of these documents are 50 years old or older so not a lot of recent data on this topic or so it would seem.
I am curious if anyone has any recent experience with using plywood or osb gusset plates on wood trusses and what was their fastener of choice and why?
I really like the idea of 3" nails that are clinched (less nails = less labor) however would a smaller diameter nail be less prone to splitting the wood members even though there are more of them and they are spaced more closely together?
I'm also considering ringshank nails since the cyclic loading on a truss might have a tendency to back the nails out over time, however the shear strength of these nails is a question needing further investigation.
For the actual gusset plate material I'm considering 1/2" DF Structural I Plywood, however I would also like to have 3/4" PLY, 19/32" PLY and 7/16" OSB as additional options. I've actually see 7/16" OSB used in a lot of home built trusses and I'm actually guilty myself of my own home brewed trusses for a small storage shed using drywall screws and 7/16" OSB (8 ft. span). Other than the strength design values are there any other caveats to using OSB in this application?
A confused student is a good student.
Nathaniel P. Wilkerson, PE