Hello,
Pictured below high speed gears in a centrifugal planetary mixer. They tend to fail very quickly, seemingly by slippage. I've been tasked with finding a way to make the system robust. Below, I've included a slow mo video of how the mixer operates, a picture of the gear that is failing both new and worn. I'll include the determinations I've come to, but I'm at a bit of a dead end when it comes to ideas past here.
Context and failure mode: It begins to slip, causing the teeth to wear down. The gears last anywhere from a week to 3-6 months, under intermittent use. (3-6 seconds at a time, total use being less than 5 minutes per day, less than 20 minutes a week. It's only the middle bevel gear that is failing, which seems to indicate to me that maybe the gear doesn't quite match the center spur.
Possible solutions that I've arrived at:
- Manufacturer's replacement: Since the mixers are cheap Chinese mixers, the warranty situation is unclear, and replacement parts are hard to attain. In addition, they do not last any longer than the original parts.
- Rework with existing gears off of the market: The gears are fairly custom and do not have any sort of equivalent on the market (that I've seen). It is a non-standard axis angle (for example, mcmaster carr only has bevel gears with a 45deg axis difference, these seem to be about 40deg).
- Add lubrication to the gear: I'm pretty sure that these are nylon, and should be self lubricating. But could adding lubrication reduce the amount of friction between the gears to make them last longer, without increasing slippage? Additionally, which grease would be viscous enough to not fling around the inside of the mixer? It's not a self contained gearbox, and it's not very easy to access the gears to add lubrication constantly.
- 3d print the gears. Traditional fdm with PLA or resin probably wouldn't result in more durable gears. Metal 3d printing leaves concerns about surface finish.
- Investment cast the gears: I don't have access to an investment casting facility with enough fidelity to reproduce the gears.
- Machine replacements (this seems to be the most long term solution): I have access to a 4-axis CNC machine, where if I could create a good enough model, a good replacement might be able to be made. In that case, would 6061 aluminum be a good candidate for the gears? What other resources are there for creating bevel gears? What kind of lubrication would be necessary? Could the center bevel gear be the only one to be manufactured, since it seems to be the primary failure point?
Thanks for reading, I'd be glad for any advice about how to progress further. Any insights on why it's failing, other possible strategies to reduce wear, and any resources for creating a replacement is welcome.
[URL unfurl="true"]https://res.cloudinary.com/engineering-com/video/upload/v1718126768/tips/447999662_8013352545355930_424334532723070885_n_ccbktf.mp4[/url]
Pictured below high speed gears in a centrifugal planetary mixer. They tend to fail very quickly, seemingly by slippage. I've been tasked with finding a way to make the system robust. Below, I've included a slow mo video of how the mixer operates, a picture of the gear that is failing both new and worn. I'll include the determinations I've come to, but I'm at a bit of a dead end when it comes to ideas past here.
Context and failure mode: It begins to slip, causing the teeth to wear down. The gears last anywhere from a week to 3-6 months, under intermittent use. (3-6 seconds at a time, total use being less than 5 minutes per day, less than 20 minutes a week. It's only the middle bevel gear that is failing, which seems to indicate to me that maybe the gear doesn't quite match the center spur.
Possible solutions that I've arrived at:
- Manufacturer's replacement: Since the mixers are cheap Chinese mixers, the warranty situation is unclear, and replacement parts are hard to attain. In addition, they do not last any longer than the original parts.
- Rework with existing gears off of the market: The gears are fairly custom and do not have any sort of equivalent on the market (that I've seen). It is a non-standard axis angle (for example, mcmaster carr only has bevel gears with a 45deg axis difference, these seem to be about 40deg).
- Add lubrication to the gear: I'm pretty sure that these are nylon, and should be self lubricating. But could adding lubrication reduce the amount of friction between the gears to make them last longer, without increasing slippage? Additionally, which grease would be viscous enough to not fling around the inside of the mixer? It's not a self contained gearbox, and it's not very easy to access the gears to add lubrication constantly.
- 3d print the gears. Traditional fdm with PLA or resin probably wouldn't result in more durable gears. Metal 3d printing leaves concerns about surface finish.
- Investment cast the gears: I don't have access to an investment casting facility with enough fidelity to reproduce the gears.
- Machine replacements (this seems to be the most long term solution): I have access to a 4-axis CNC machine, where if I could create a good enough model, a good replacement might be able to be made. In that case, would 6061 aluminum be a good candidate for the gears? What other resources are there for creating bevel gears? What kind of lubrication would be necessary? Could the center bevel gear be the only one to be manufactured, since it seems to be the primary failure point?
Thanks for reading, I'd be glad for any advice about how to progress further. Any insights on why it's failing, other possible strategies to reduce wear, and any resources for creating a replacement is welcome.
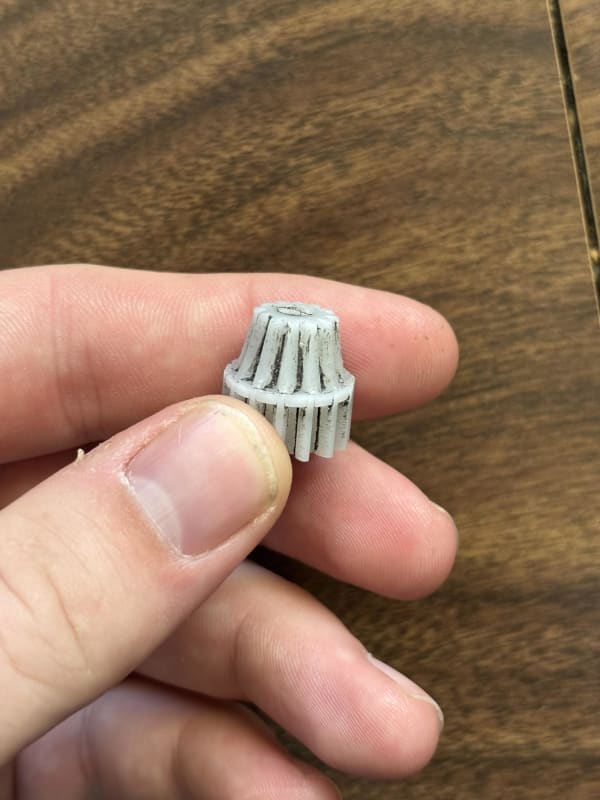
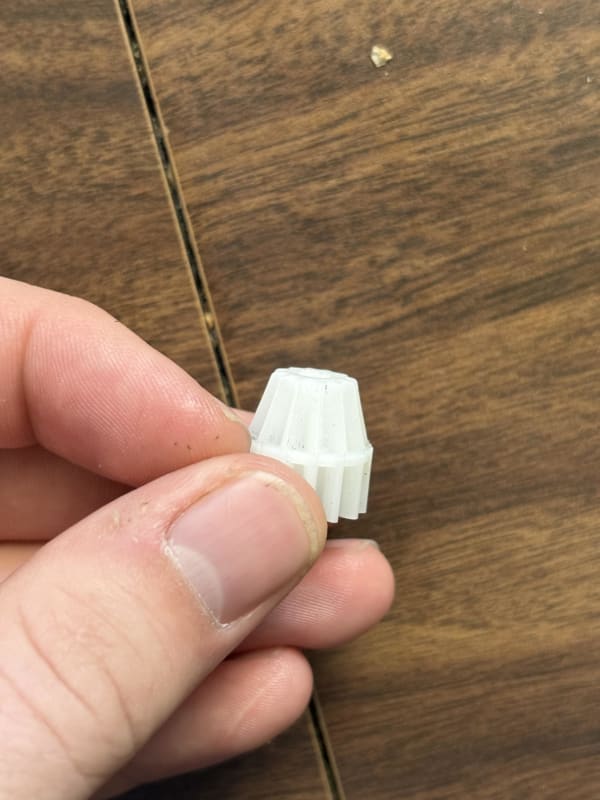