GregLocock
Automotive
- Apr 10, 2001
- 23,723
Just a quick look at TMDs, which came up elsewhere. In this case I am looking at the normal automotive case, where a large body is excited directly by a force, and we then bolt on a TMD. Typical example is the harmonic damper on the crankshaft, used to suppress torsional vibrations, and bending in some cases, or the extension housing damper on rear wheel drive cars to suppress powertrain bending. Some cars have 6 or more.
Here's the system
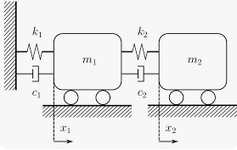
M1 is the engine or other large object, m2 is the TMD.
I'll start with the classic approach where the TMD is tuned to the problem frequency of the main system, with no damping for the TMD. Great response at 5Hz, pretty lousy at the 2 resonances.
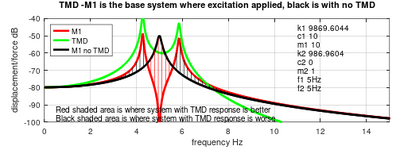
Now add some damping to c2
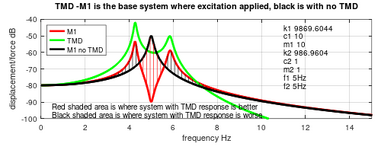
So there's some residual response at 5 Hz, but the 2 split resonances are down.
Now change m2 to 0.3, this should reduce the frequency range between the two red peaks.
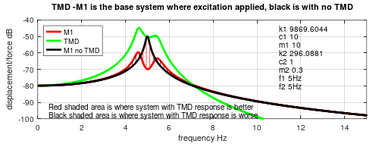
OK, that worked. go back to 1.0 kg for m2, and try under tuning it, so instead of 5 Hz, make it 4 hz
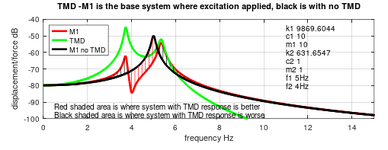
That's good, we've now got suppression across quite a broad range. Or try overtuning it, to say 6 Hz
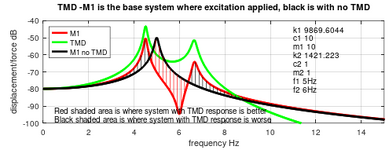
and increase c2 to 3, to try and get the red peaks down
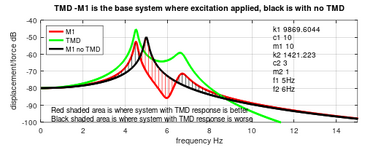
Incidentally a mass ratio of 0.1 is quite high, that's why you need to mount the TMD at an antinode.
Here's the system
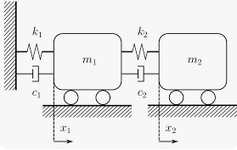
M1 is the engine or other large object, m2 is the TMD.
I'll start with the classic approach where the TMD is tuned to the problem frequency of the main system, with no damping for the TMD. Great response at 5Hz, pretty lousy at the 2 resonances.
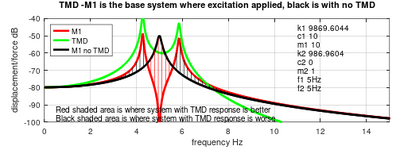
Now add some damping to c2
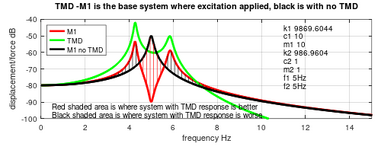
So there's some residual response at 5 Hz, but the 2 split resonances are down.
Now change m2 to 0.3, this should reduce the frequency range between the two red peaks.
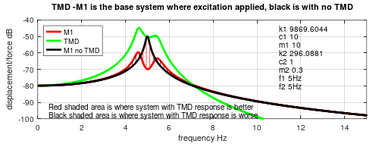
OK, that worked. go back to 1.0 kg for m2, and try under tuning it, so instead of 5 Hz, make it 4 hz
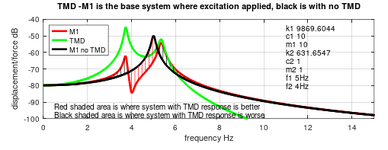
That's good, we've now got suppression across quite a broad range. Or try overtuning it, to say 6 Hz
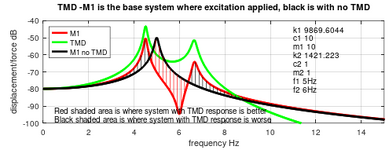
and increase c2 to 3, to try and get the red peaks down
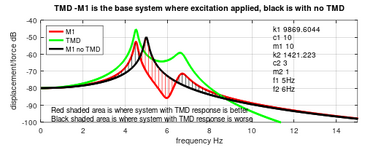
Incidentally a mass ratio of 0.1 is quite high, that's why you need to mount the TMD at an antinode.