Hi all
I'm currently balancing micro-turbine rotors using 2 plane balancing method. ISO1940 G2.5 requires a quality balance limit of 0.033mm.gram per bearing location in my case (100,000rpm), which I'm finding near impossible. Is ISO1940 limits a bit of an overkill? The best I can physically achieve is an order of magnitude higher (0.33mm.gram).
I have updated with an image similar to what I'm using. It appears that there is always some residual mechanical vibes present. The bearings have been changed to quality Japanese bearings which have little play in them. Also the balance cradle has some play along the shaft axis so the cradle isn't too over-constrained. The turbine is driven by compressed air at around 3000 RPM. I find this works well enough to see vibes in the system.
.
thanks
Dynaman.
I'm currently balancing micro-turbine rotors using 2 plane balancing method. ISO1940 G2.5 requires a quality balance limit of 0.033mm.gram per bearing location in my case (100,000rpm), which I'm finding near impossible. Is ISO1940 limits a bit of an overkill? The best I can physically achieve is an order of magnitude higher (0.33mm.gram).
I have updated with an image similar to what I'm using. It appears that there is always some residual mechanical vibes present. The bearings have been changed to quality Japanese bearings which have little play in them. Also the balance cradle has some play along the shaft axis so the cradle isn't too over-constrained. The turbine is driven by compressed air at around 3000 RPM. I find this works well enough to see vibes in the system.
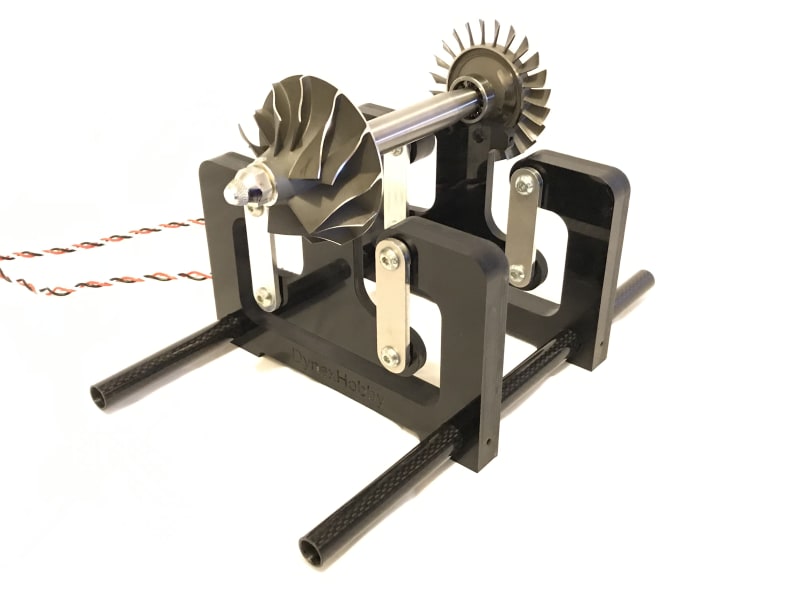
thanks
Dynaman.