-
1
- #1
thread404-468702
Hi,
We have already build the turning device. The post where I asked is closed
I just wanted to share some pictures and say thanks to everybody
cheers,
Hi,
We have already build the turning device. The post where I asked is closed
I just wanted to share some pictures and say thanks to everybody
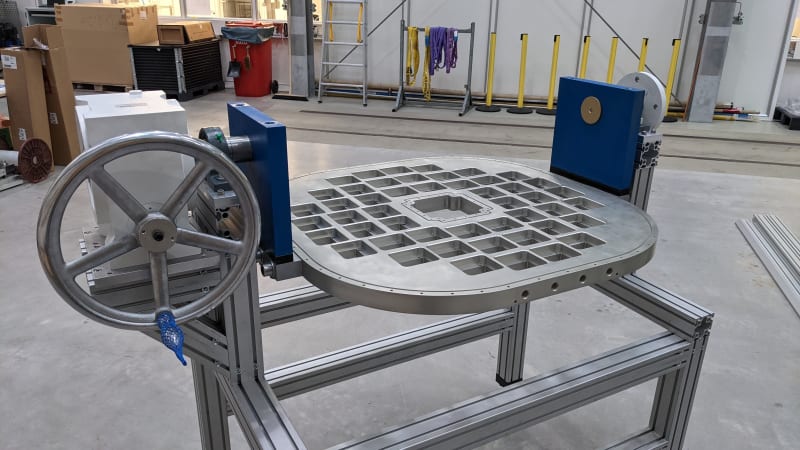
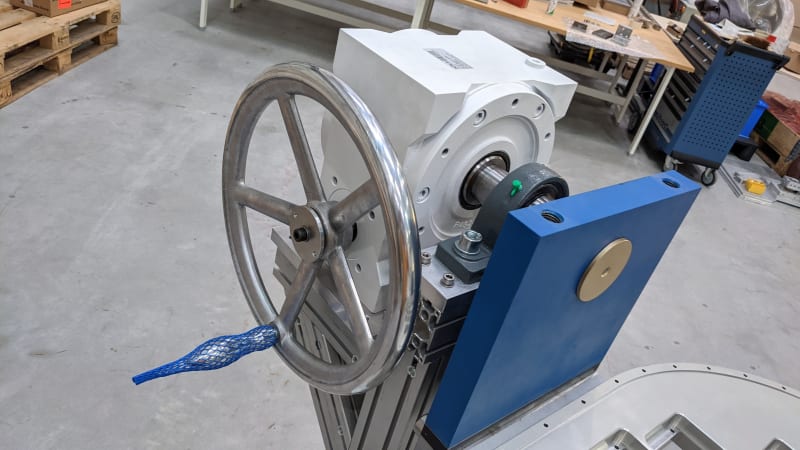
cheers,