Amin Behzadi
Mechanical
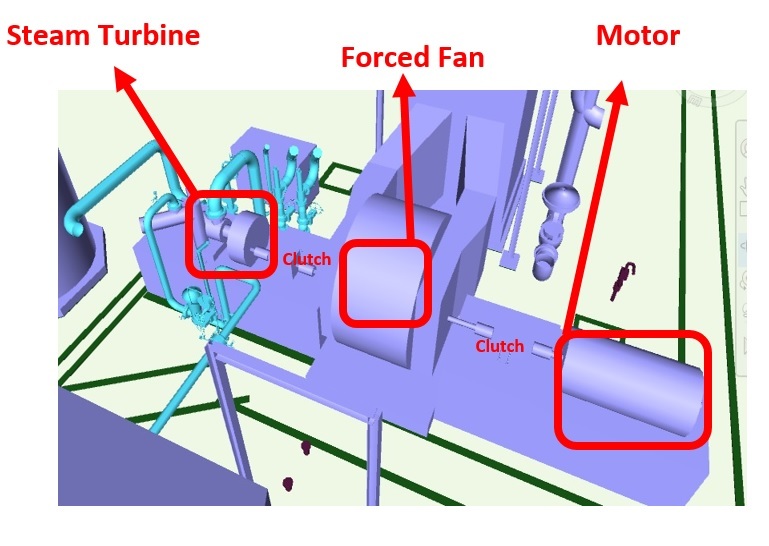
I have a forced fan that has two equipment as driver, a electric motor (start-up) and a steam turbine (permanent). I want to know which equipment is better to set as stationary for shaft aligning? What is the best procedure? For example set fan as stationary and align turbine and motor based on it?