sticksandtriangles
Structural
- Apr 7, 2015
- 490
Recently I was working with some really large loads and trying to deal with punching shear on thick concrete elements.
I worked the ACI equations for punching shear and I needed (32) #5, bars, (8) legs*4 sides, at my critical perimeter, at a spacing of 6"oc.
Traditional examples of punching shear reinforcing always show this thin flat slabs, typically using stud rails that are centered on the column width and then stay within the same column dimensions as they move away from the column.
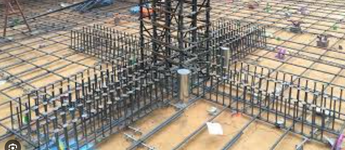
I aimed to match this traditional layout in my heavily loaded thick foundation.
See option 1 below:
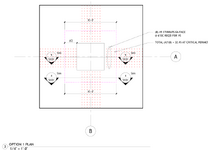
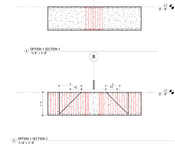
I showed this to a colleague and they asked to splay these out over the critical perimeter, which I initially thought would be fine, but now I have some concerns.
Option 2:
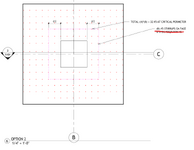
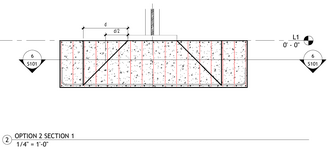
Option 2 has the same amount of reinforcing at the critical perimeter, 8 #5 per face, but the spacing can be greatly reduced, to around 1.25ft in each direction with this setup.
I think the code really is pushing for option 1 as is traditional with shear stud rail layout, but I wanted others opinions.
ACI 318-19 now works in shear stress for vs, but I think the heart of the equation is finding the # of bars that cross the d away failure plane as shown in the red region below:
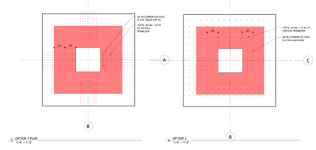
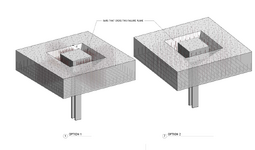
Option 2 starts to make a come back in raw steel area after d/2 away into the d region, but I don't think it is enough typically. Also the stress concentrations are highest near the column support, so it feels a bit dubious to pick up extra capacity away from the column?
Had a bit too much fun making the images as you can see. Modelling rebar in revit seems pretty slick.
I worked the ACI equations for punching shear and I needed (32) #5, bars, (8) legs*4 sides, at my critical perimeter, at a spacing of 6"oc.
Traditional examples of punching shear reinforcing always show this thin flat slabs, typically using stud rails that are centered on the column width and then stay within the same column dimensions as they move away from the column.
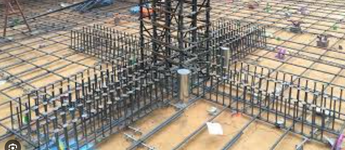
I aimed to match this traditional layout in my heavily loaded thick foundation.
See option 1 below:
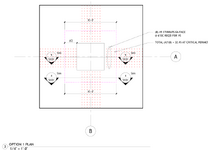
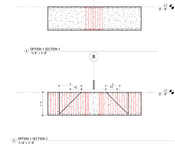
I showed this to a colleague and they asked to splay these out over the critical perimeter, which I initially thought would be fine, but now I have some concerns.
Option 2:
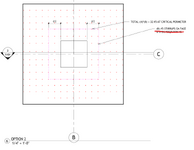
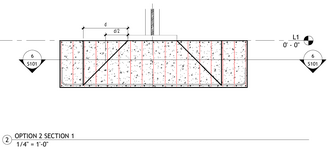
Option 2 has the same amount of reinforcing at the critical perimeter, 8 #5 per face, but the spacing can be greatly reduced, to around 1.25ft in each direction with this setup.
I think the code really is pushing for option 1 as is traditional with shear stud rail layout, but I wanted others opinions.
ACI 318-19 now works in shear stress for vs, but I think the heart of the equation is finding the # of bars that cross the d away failure plane as shown in the red region below:
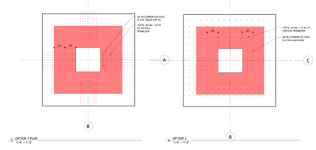
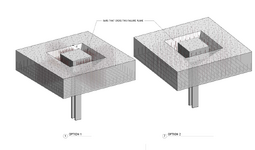
Option 2 starts to make a come back in raw steel area after d/2 away into the d region, but I don't think it is enough typically. Also the stress concentrations are highest near the column support, so it feels a bit dubious to pick up extra capacity away from the column?
Had a bit too much fun making the images as you can see. Modelling rebar in revit seems pretty slick.