In a two slab (supported on walls), if designing manually using strip methods, should the shear reinforcement required for x direction (Asx) be summed with the shear reinforcement required for the y direction (Asy). The total area (As) be applied to the critical regions?
Otherwise, is it safe to simply design a strip for the maximum shear force (whether its in the x or y direction) without summing up the As.shear required for both directions?
This is an issue that has caused a lot of confusion in my office with many clashing opinions. In a strut and tie model, each direction has a vertical tension force that needs to be resisted, so it does make sense to me to design the slab for a sum of the shear. See diagrams.
Otherwise, is it safe to simply design a strip for the maximum shear force (whether its in the x or y direction) without summing up the As.shear required for both directions?
This is an issue that has caused a lot of confusion in my office with many clashing opinions. In a strut and tie model, each direction has a vertical tension force that needs to be resisted, so it does make sense to me to design the slab for a sum of the shear. See diagrams.
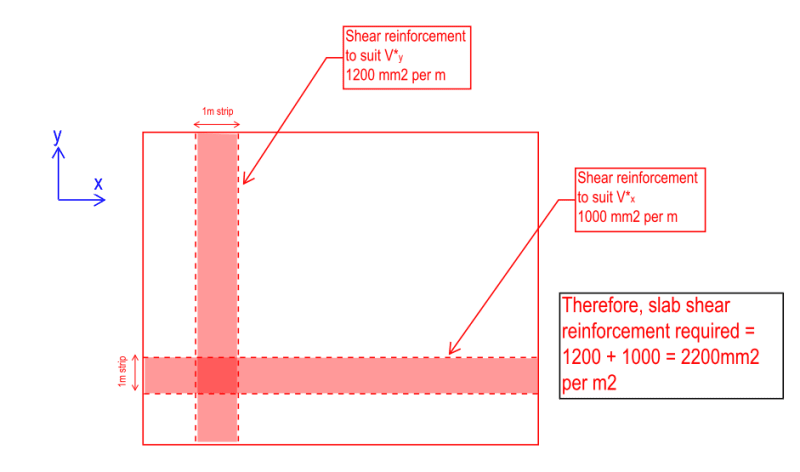
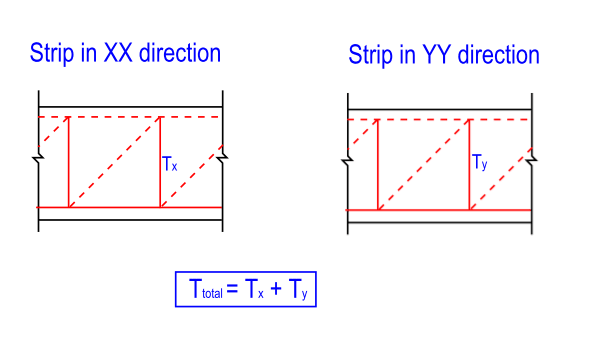