Hi,
The way I analyze this warehouse subjecting to wind in say Y direction is using Y direction walls as supports and the roof structure as a truss to transfer the lateral loads to these walls. I would expect large reaction at end due to its span. Now my question is, will the very first bolt for pfc wind beam to wall sufficient to carry this load? (refer to the detail A below. raker-wall, raker-wind beam connection etc are not shown). I have done the check and find the capacity lower than design reaction but I have seen this detail being used quite a lot. So how do you normally detail this?
The way I analyze this warehouse subjecting to wind in say Y direction is using Y direction walls as supports and the roof structure as a truss to transfer the lateral loads to these walls. I would expect large reaction at end due to its span. Now my question is, will the very first bolt for pfc wind beam to wall sufficient to carry this load? (refer to the detail A below. raker-wall, raker-wind beam connection etc are not shown). I have done the check and find the capacity lower than design reaction but I have seen this detail being used quite a lot. So how do you normally detail this?
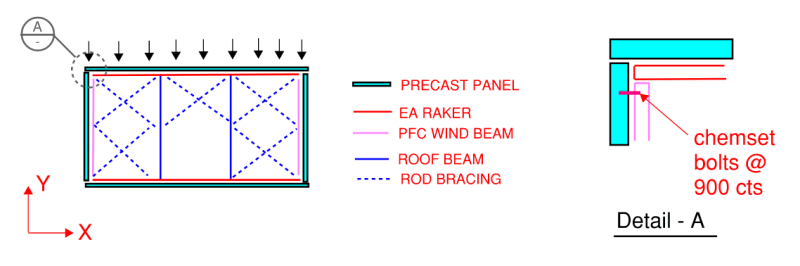