LAB01
Structural
- Dec 8, 2023
- 3
How do you handle ugly welds when you are analyzing existing connections? Do you have personal safety factors if you are not happy with how they look, or do you just assume that they have the same strength as a good weld. See pic attached.
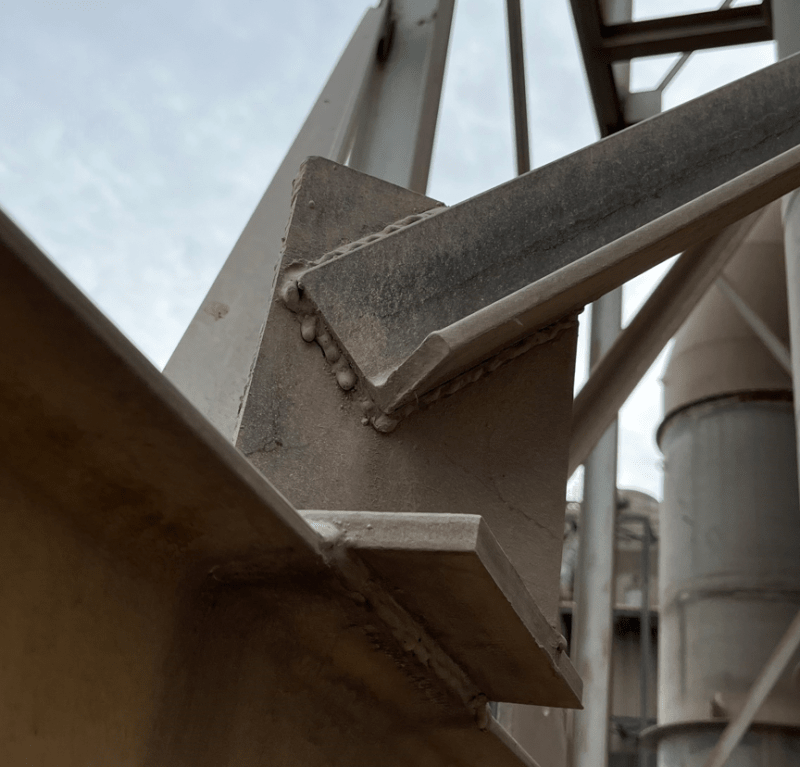