CANeng11
Civil/Environmental
- Feb 18, 2015
- 114
We have been asked to provide a repair detail for a walkout retaining wall (see attached picture). We don't have details on the reinforcement or footings, but the wall has a bow to it and it's about 10 years old. It's about 30 feet long, 6 feet high and 8 inch thick concrete (icf). The contractor would like to pour a slab in the bottom to restrain the bottom of the wall, but he is unsure how to reinforce the top of the wall. I'm wondering if anyone has any ideas?
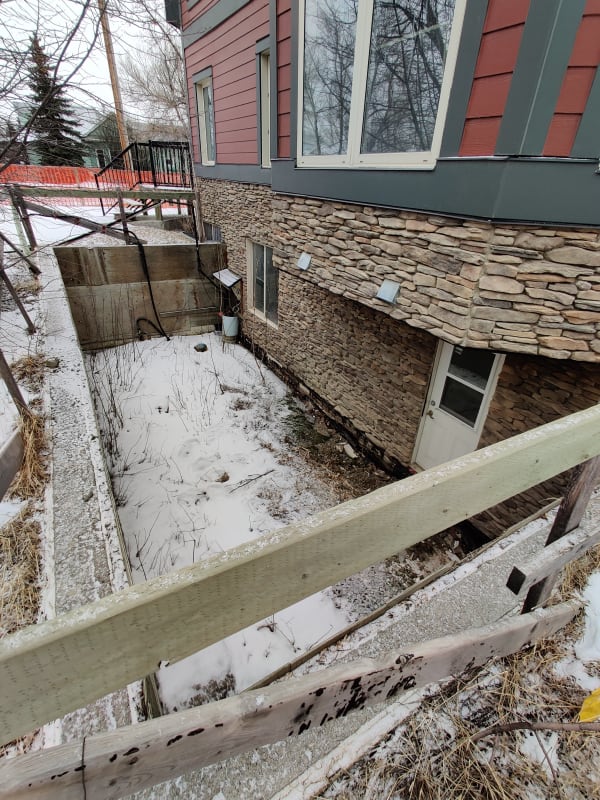