xhuydo
Mechanical
- Jan 18, 2017
- 7
Thank you for taking the time and reading my post. I very much appreciate your help.
I am getting bubbles into my pipe system and wanted to know how they are forming and what I can do to remediate.
The flow begins at the a reservoir holding water that is open to the atmosphere. Water flows from the bottom via a gated valve and into a centrifugal pump. The flow is directed up and then down. The flow passes turbine flow meter, pressure gauge, and exits from an acrylic nozzle. The plumbing consist of 3/4" ID plastic tubing, and 1" ID PVC. The nozzle has a 1/5" square exit. The nozzle attaches by a mount. The mount screws onto a threaded PVC adapter and then nozzle is essentially clamped on.
At 8 liters per minute(lpm), I am observing small bubbles around the PVC adapter and acrylic nozzle connection. Then as I increase the flow rate up to approximately 9 lpm a large bubble (approximately 1") forms.
My initial guess is that I have air leak in the nozzle mount and nozzle area. I placed an o-ring in between the nozzle and the nozzle mount but the issue still persist.
I apologize for such a long post. I tried to be as descriptive as possible. Please let me know if I need to clarify anything.
I am getting bubbles into my pipe system and wanted to know how they are forming and what I can do to remediate.
The flow begins at the a reservoir holding water that is open to the atmosphere. Water flows from the bottom via a gated valve and into a centrifugal pump. The flow is directed up and then down. The flow passes turbine flow meter, pressure gauge, and exits from an acrylic nozzle. The plumbing consist of 3/4" ID plastic tubing, and 1" ID PVC. The nozzle has a 1/5" square exit. The nozzle attaches by a mount. The mount screws onto a threaded PVC adapter and then nozzle is essentially clamped on.
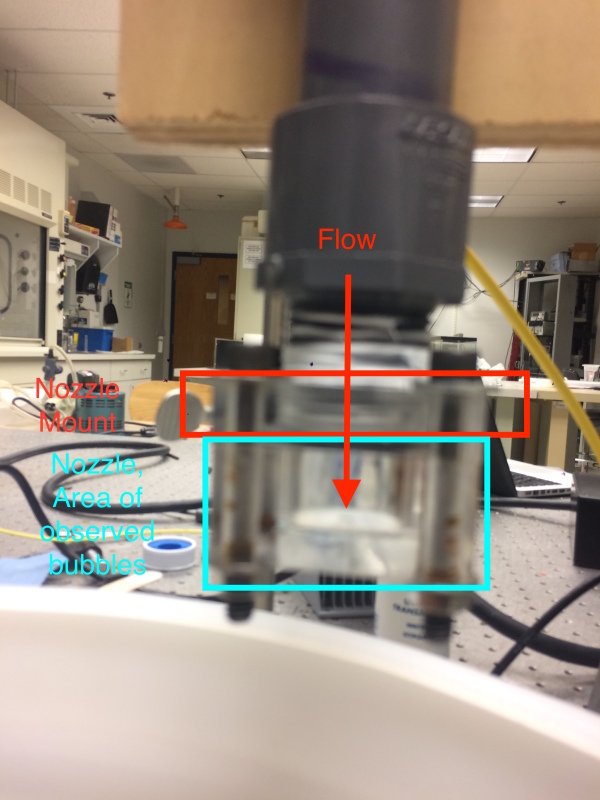
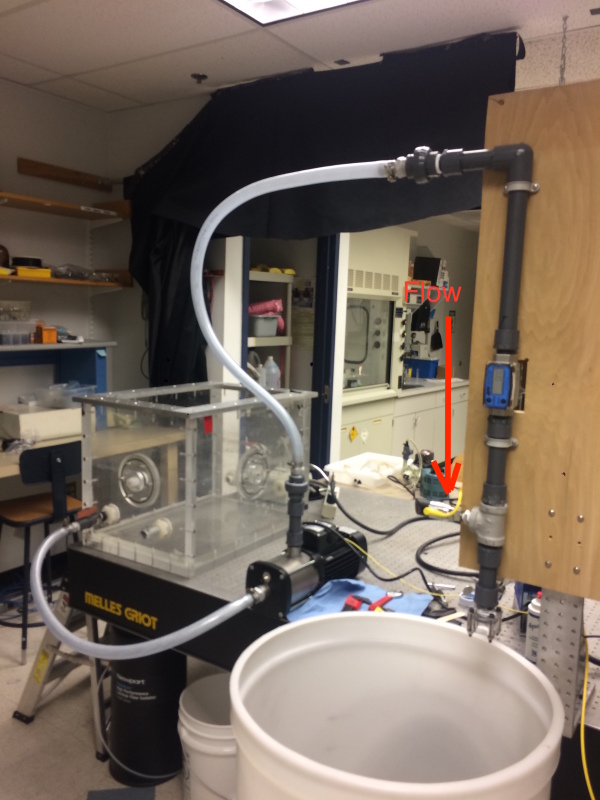
At 8 liters per minute(lpm), I am observing small bubbles around the PVC adapter and acrylic nozzle connection. Then as I increase the flow rate up to approximately 9 lpm a large bubble (approximately 1") forms.
My initial guess is that I have air leak in the nozzle mount and nozzle area. I placed an o-ring in between the nozzle and the nozzle mount but the issue still persist.
I apologize for such a long post. I tried to be as descriptive as possible. Please let me know if I need to clarify anything.