akhb76
Bioengineer
- Jul 27, 2015
- 2
Hi,
I'm R&D manager of a bone implant manufacturing company,
We recently produced 1000 screws using Thread rolling method but they didn't get approved and we recalled them,
The reason was 'Residual stress' how to release the stress by non-thermal method.
Thanks
I'm R&D manager of a bone implant manufacturing company,
We recently produced 1000 screws using Thread rolling method but they didn't get approved and we recalled them,
The reason was 'Residual stress' how to release the stress by non-thermal method.
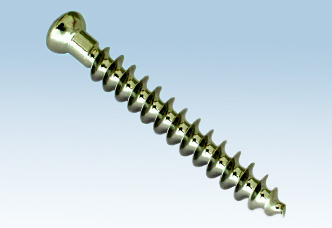
Thanks