Enable
Structural
- Jan 15, 2021
- 788
I have a vertical formwork design where I would like to use aluma beam whalers, and for constructability reasons I would like to invert the beam. That is, large side on loading member and small nailing edge on support.
The literature on the beams doesn’t give anything on this and I haven’t been able to get through to engineering. It’s a homogenous material so you’d think I shouldn’t have any concerns about this but since I don’t design with aluminum here are my thoughts (FYI span is 1.2 meters so these beams should be shear controlled and the buckling concerns may be moot):
A) By inverting the beam I am changing the primary compression flange (though as a continuous beam it’ll switch). If the beams have local buckling issues inverting the beam may not make the span load tables applicable. Same doubles for brace location requirements to deal with LTB (doubtful but still)
B) Bearing area is significantly less on the nailing strip side
Anecdotally, I have formed using inverted alumas before when in a pinch. But never with the kind of loads I am designing this for. Time is essential here so any thoughts would be much appreciated!
The literature on the beams doesn’t give anything on this and I haven’t been able to get through to engineering. It’s a homogenous material so you’d think I shouldn’t have any concerns about this but since I don’t design with aluminum here are my thoughts (FYI span is 1.2 meters so these beams should be shear controlled and the buckling concerns may be moot):
A) By inverting the beam I am changing the primary compression flange (though as a continuous beam it’ll switch). If the beams have local buckling issues inverting the beam may not make the span load tables applicable. Same doubles for brace location requirements to deal with LTB (doubtful but still)
B) Bearing area is significantly less on the nailing strip side
Anecdotally, I have formed using inverted alumas before when in a pinch. But never with the kind of loads I am designing this for. Time is essential here so any thoughts would be much appreciated!
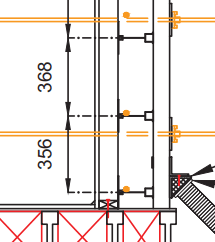