I'm working on a retractable handle, vertically up/down, and looking for the best way to keep it from falling down when its pulled up to any position. Normal approach would be to use a spring but I'm limited as far as space goes and can't fit a spring under the shaft or inside the shaft where it would extend against the inner base. So, I'm thinking of using perhaps an oring, or another friction object, which sits near the top and makes contact with the shaft putting enough pressure so that it doesn't fall down on its own.
Below is a rough drawing of the concept, the green circles are where the oring would be placed making contact with the shaft. All materials involved will be anodized aluminum. The handle will be fairly light, maybe couple hundred grams at most. It will be moved maybe several times a day which isn't much but I'm still concerned about longevity and how long it will last before it starts to lose tension against the shaft. Perhaps oring is not the best for this?
Any suggestions/ideas would be appreciated.
Thank you!
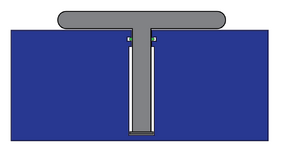
Below is a rough drawing of the concept, the green circles are where the oring would be placed making contact with the shaft. All materials involved will be anodized aluminum. The handle will be fairly light, maybe couple hundred grams at most. It will be moved maybe several times a day which isn't much but I'm still concerned about longevity and how long it will last before it starts to lose tension against the shaft. Perhaps oring is not the best for this?
Any suggestions/ideas would be appreciated.
Thank you!
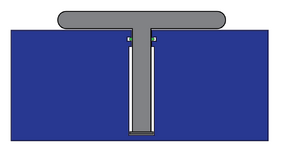