PaulKraemer
Electrical
Hi,
In the diagram below going from right-to-left, I have a type-J thermocouple mounted inside what I describe as the "Applicator". Two conductor Type-J thermocouple cable is used to connect the thermocouple (+) and (-) leads to pins on the 9-pin connector. Regular wire (not thermocouple wire) is used inside the heated hose (which is about 12 feet long) to connect the thermocouple signals ((+) and (-)) to pins on the sixteen pin connector. I have to make the connection to get the thermocouple signal from the 16-pin connector to the Temperature controller. I know that for the best accuracy with thermocouples, it is recommended to use only thermocouple cable throughout the entire connection. This being said, the heated hose is a standard part I buy from a 3rd party supplier. This 3rd party supplier is unable (or unwilling) to supply heated hoses with thermocouple cable for this connection instead of regular wire. With this being the case, as I believe my accuracy will already be compromised due to the connection through the heated hose, I am wondering if there is any advantage to be gained by using thermocouple cable for the connection from the temperature controller to the 16-pin connector. I find it easier to work with regular wire as opposed to thermocouple cable, and I always feel like the crimp-on pins and sockets I use with my 16-pin connectors attach more reliably to #18 AWG stranded wire as opposed to typically #24 AWG solid conductor thermocouple cable. For these reasons, I am leaning towards using #18 AWG stranded wire in this case, but if anyone here tells me there is some advantage to be gained by using thermocouple cable (even though the signal will pass through regular wire inside the heated hose), I will will do so.
Any suggestions or advice will be greatly appreciated.
Thanks in advance,
Paul
In the diagram below going from right-to-left, I have a type-J thermocouple mounted inside what I describe as the "Applicator". Two conductor Type-J thermocouple cable is used to connect the thermocouple (+) and (-) leads to pins on the 9-pin connector. Regular wire (not thermocouple wire) is used inside the heated hose (which is about 12 feet long) to connect the thermocouple signals ((+) and (-)) to pins on the sixteen pin connector. I have to make the connection to get the thermocouple signal from the 16-pin connector to the Temperature controller. I know that for the best accuracy with thermocouples, it is recommended to use only thermocouple cable throughout the entire connection. This being said, the heated hose is a standard part I buy from a 3rd party supplier. This 3rd party supplier is unable (or unwilling) to supply heated hoses with thermocouple cable for this connection instead of regular wire. With this being the case, as I believe my accuracy will already be compromised due to the connection through the heated hose, I am wondering if there is any advantage to be gained by using thermocouple cable for the connection from the temperature controller to the 16-pin connector. I find it easier to work with regular wire as opposed to thermocouple cable, and I always feel like the crimp-on pins and sockets I use with my 16-pin connectors attach more reliably to #18 AWG stranded wire as opposed to typically #24 AWG solid conductor thermocouple cable. For these reasons, I am leaning towards using #18 AWG stranded wire in this case, but if anyone here tells me there is some advantage to be gained by using thermocouple cable (even though the signal will pass through regular wire inside the heated hose), I will will do so.
Any suggestions or advice will be greatly appreciated.
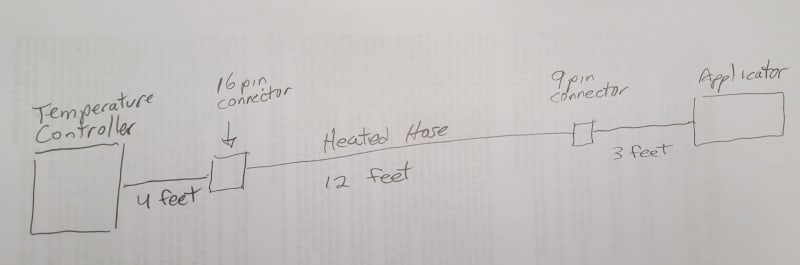
Thanks in advance,
Paul