drennon236
Civil/Environmental
Say I have two cylindrical surfaces in contact (in reality there are three) and I am using surface-to-surface, penalty method and hard contact:
The cylinders are sticking, but when I check maximum penetration I see that it comes to 4.5e-09 m. Meaning there is very small amount of penetration.
However, if I use "hard contact" - shouldnt the pressure develop like down below? Meaning no penetration. Because right now I get a small amount of penetration, also normal pressure of 5 MPa develops due to the penetration that occurs. The compressive strength of my part is 120 MPa, so this gives an error of approximately 4% - Is this acceptable? Or do I have to use Lagrange method instead of penalty? My project manager said he wants a penetration of 0, but im not sure this is possible without significantly increasing computational time.
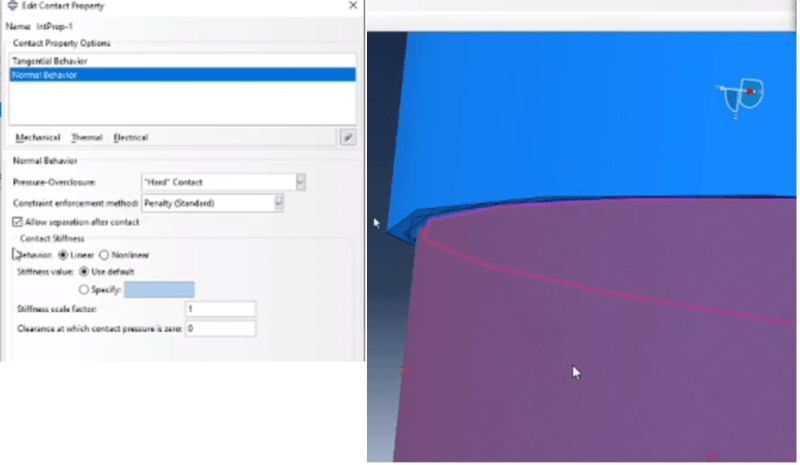
The cylinders are sticking, but when I check maximum penetration I see that it comes to 4.5e-09 m. Meaning there is very small amount of penetration.
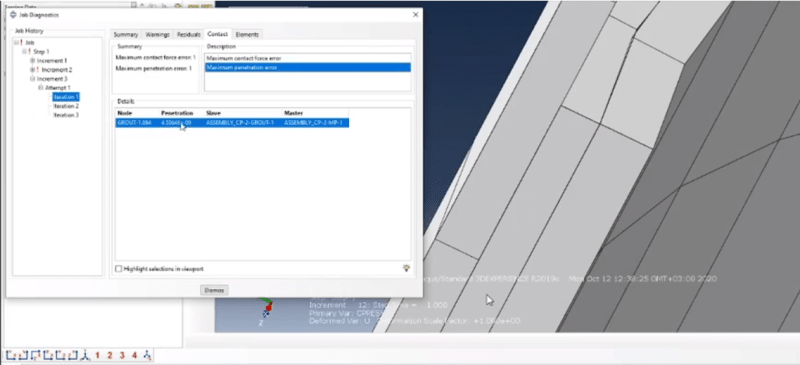
However, if I use "hard contact" - shouldnt the pressure develop like down below? Meaning no penetration. Because right now I get a small amount of penetration, also normal pressure of 5 MPa develops due to the penetration that occurs. The compressive strength of my part is 120 MPa, so this gives an error of approximately 4% - Is this acceptable? Or do I have to use Lagrange method instead of penalty? My project manager said he wants a penetration of 0, but im not sure this is possible without significantly increasing computational time.
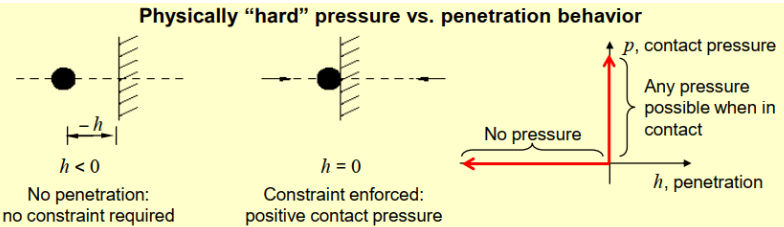