Viktoras
Industrial
- May 12, 2023
- 2
Hello,
I'm using a vacuum turbine in my factory to collect dusts from several machines
factory produces kitchens. Machines are CNC nestings.
For 1,5years system was working fine. And one day the turbine motor burned.
We have rewired (local service) the motor, and it worked for 2 weeks and then the stator burned again.
we have rewired (local service) again, but this time added additional protection
* (thermo-couple and thermo-resistor)
* amperemeter to constantly measure the current in each contour (it is triangle wired for 380V)
This time Motor worked for 15min. then the protection has kicked-in
We are using Garden Denver turbine 2BH1 943-7GH37 with a 21kw Siemens motor.
-
What we know:
1. The outer system (ducts, separators, pressure valves, exhaust) has not changed
2. Before rewire it used 34-35A in each of stator contours (while turbine was integrated in system)
3. After 1st rewire it used 24-25A in each of stator contours (while turbine was integrated in system)
4. After 2nd rewire it uses 43-44A in each of stator contours (while turbine was integrated in system)
(and uses 24A while detached from the system)
5. The pressure in the system remained the same -240mbar (which is ok for this turbine)
6. Motor is wired in triangle for 380V
7. The resistance in each contour is ~0,5ohm (today)
8. The isolation is fine, the reistance is like 2Giga ohms
I suspect that the motor lost its torque after 2nd rewire
The question is - which parameters might be lost in second rewiring process, and can they be restored in 3rd rewire?
Many Thanks
I'm using a vacuum turbine in my factory to collect dusts from several machines
factory produces kitchens. Machines are CNC nestings.
For 1,5years system was working fine. And one day the turbine motor burned.
We have rewired (local service) the motor, and it worked for 2 weeks and then the stator burned again.
we have rewired (local service) again, but this time added additional protection
* (thermo-couple and thermo-resistor)
* amperemeter to constantly measure the current in each contour (it is triangle wired for 380V)
This time Motor worked for 15min. then the protection has kicked-in
We are using Garden Denver turbine 2BH1 943-7GH37 with a 21kw Siemens motor.
-
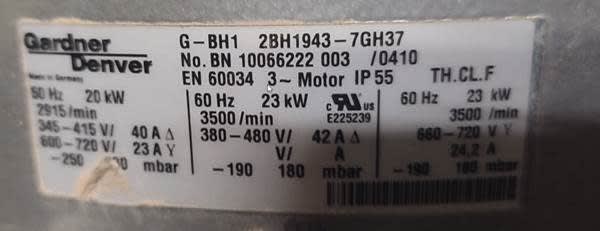
What we know:
1. The outer system (ducts, separators, pressure valves, exhaust) has not changed
2. Before rewire it used 34-35A in each of stator contours (while turbine was integrated in system)
3. After 1st rewire it used 24-25A in each of stator contours (while turbine was integrated in system)
4. After 2nd rewire it uses 43-44A in each of stator contours (while turbine was integrated in system)
(and uses 24A while detached from the system)
5. The pressure in the system remained the same -240mbar (which is ok for this turbine)
6. Motor is wired in triangle for 380V
7. The resistance in each contour is ~0,5ohm (today)
8. The isolation is fine, the reistance is like 2Giga ohms
I suspect that the motor lost its torque after 2nd rewire
The question is - which parameters might be lost in second rewiring process, and can they be restored in 3rd rewire?
Many Thanks