Caliberdesign
Mechanical
- Jul 20, 2016
- 6
Hi Guys,
I am working with a prototype in which we designed a valve seating against an Oring. Please see below
To seat the valve there is a spring force and a pressure force as indicated by the arrows. The valve works well for our pressure range 0-600 Psi. The problem is when a colleague tried to scale up the design 2x the diameter and the pressure in the scaled version will not hold above 350 PSI. Scaled up version below.
My gut feel would have said this new scaled design should work also. We could not scale the seating spring proportionally but in theory it will be the air pressure that mainly acts to set the valve. Spring seating force around 7 Kg. Air pressure seating force at 500 PSI is around 30kg for the scaled version and 18kg for the non-scaled version. We used a ratio of the circumference lengths to scale up the seating pressure force.
I have heard i should aim for a pressure between the two faces sealing faces of 2x the pressure i am trying to seal against. I this correct? It is a little hard to calculate as is it sealing on an Oring and the exact deformation on the sealing area is unknown. The other issue could be with air escaping around the back of the Oring. The Oring in the scaled version was not given as much squash in the cross-section. Around .3mm for a 5.33mm CS Oring. The working design has a 0.5mm squash in a 5mm CS.
Would be very interested to hear any thoughts. Am i missing anything obvious as to why the scaled version is not working?
Many Thanks,
I am working with a prototype in which we designed a valve seating against an Oring. Please see below
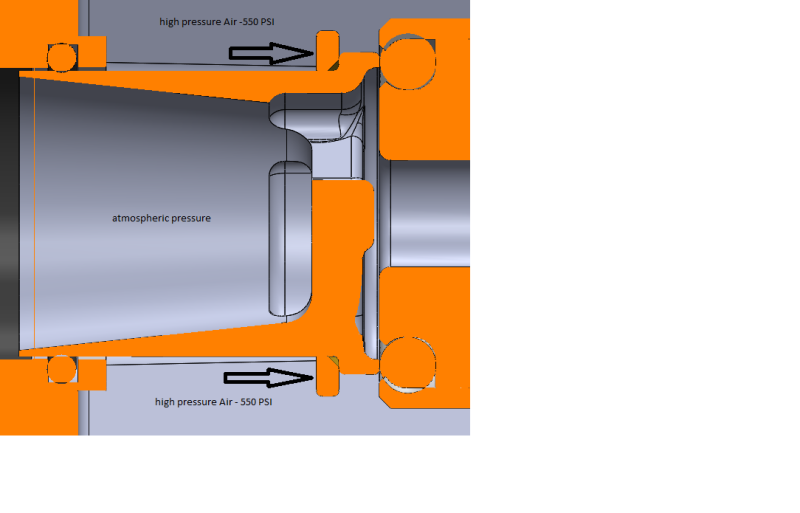
To seat the valve there is a spring force and a pressure force as indicated by the arrows. The valve works well for our pressure range 0-600 Psi. The problem is when a colleague tried to scale up the design 2x the diameter and the pressure in the scaled version will not hold above 350 PSI. Scaled up version below.
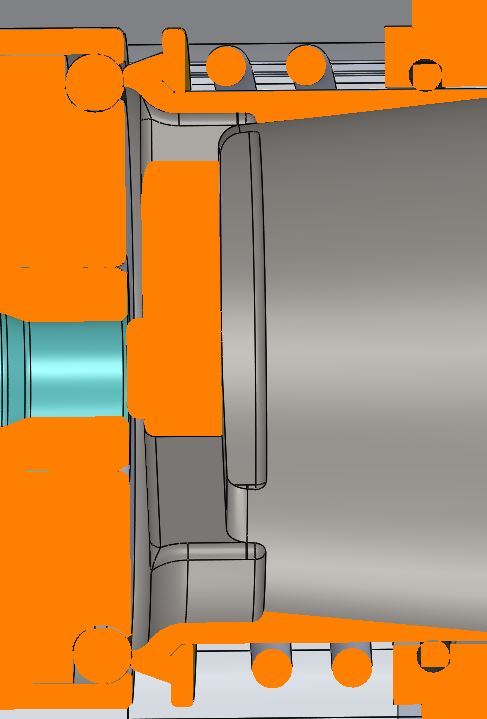
My gut feel would have said this new scaled design should work also. We could not scale the seating spring proportionally but in theory it will be the air pressure that mainly acts to set the valve. Spring seating force around 7 Kg. Air pressure seating force at 500 PSI is around 30kg for the scaled version and 18kg for the non-scaled version. We used a ratio of the circumference lengths to scale up the seating pressure force.
I have heard i should aim for a pressure between the two faces sealing faces of 2x the pressure i am trying to seal against. I this correct? It is a little hard to calculate as is it sealing on an Oring and the exact deformation on the sealing area is unknown. The other issue could be with air escaping around the back of the Oring. The Oring in the scaled version was not given as much squash in the cross-section. Around .3mm for a 5.33mm CS Oring. The working design has a 0.5mm squash in a 5mm CS.
Would be very interested to hear any thoughts. Am i missing anything obvious as to why the scaled version is not working?
Many Thanks,