Hello guys!
First of all, as this is my first post, a small bio: I am a 29 yo Portuguese Mec Engineer with a master's in Mechatronics living in the Netherlands. I have good knowledge in PLC programming, quite handy with workshop tools (spent 2.5 years full time as a knife maker @cruzadosblades on IG!) and helped during my teenage years repairing home appliances with my dad. One thing I know close to nothing about is plumbing, pumps and valves.
We are adapting a typical front loading washing machine to dye stuff, by mixing the intake water with ink. After wiring it up through a PLC, everything works as intended but all the batch fluid gets drained at the end with pigment to spare. Soo, as the next step, we are looking for a way to reuse it for more than once: this involves a 3/2 valve on the pump outlet, to either transport the fluid to an overhead tank that's sitting on top of the machine or to a drain pipe, but also a 2/2 valve on the bottom of the tank so that, when powered, will open and allow the fluid sitting in that overhead tank to flow back to the drum of the machine. Fairly simple to all of you, but me!
I had some spare valves that I tried but, after they didn't allow fluid passage when energized, I researched a little and found out they were indirect acting, i.e., they require dP of at least 0.2bar to fully open. I am left with semi-direct, direct solenoids or changing to a motorized ball valve.
Some extra details:
- No fast acting required
- Fluid is a solution of water and non corrosive liquid ink with no solid pigments, at a maximum temperature of 80C (about 172F)
- Pipe ID for the outlet of the gravity fed 2/2 valve is 10mm (4 inches), but for the 3/2 valve it is still undefined. I can only assume that if I get a 20mm bore valve feeding into a 10mm ID pipe, it would be overkill. Correct me if I am wrong!
So, my questions are:
1. Would a semi-direct valve work better than a direct? Are you 100% positive it would work with such low dP?
2. Would a hollow ball valve induce less pressure drop? I am using the WMachine pump (with the inneficient rectangular paddle-like impeller) which already struggles to maintain a decent flow of water for the purpose since I had to route the outlet a bit higher and these pumps aren't really known for having a high head. Solenoid valve internals typically have a higher pressure drop.
If there's something I am unaware of, please, feel absolutely free to point it out! Oh, and sorry for the long post!
Have a great day.
Cheers,
Adriano Pires.
First of all, as this is my first post, a small bio: I am a 29 yo Portuguese Mec Engineer with a master's in Mechatronics living in the Netherlands. I have good knowledge in PLC programming, quite handy with workshop tools (spent 2.5 years full time as a knife maker @cruzadosblades on IG!) and helped during my teenage years repairing home appliances with my dad. One thing I know close to nothing about is plumbing, pumps and valves.
We are adapting a typical front loading washing machine to dye stuff, by mixing the intake water with ink. After wiring it up through a PLC, everything works as intended but all the batch fluid gets drained at the end with pigment to spare. Soo, as the next step, we are looking for a way to reuse it for more than once: this involves a 3/2 valve on the pump outlet, to either transport the fluid to an overhead tank that's sitting on top of the machine or to a drain pipe, but also a 2/2 valve on the bottom of the tank so that, when powered, will open and allow the fluid sitting in that overhead tank to flow back to the drum of the machine. Fairly simple to all of you, but me!
I had some spare valves that I tried but, after they didn't allow fluid passage when energized, I researched a little and found out they were indirect acting, i.e., they require dP of at least 0.2bar to fully open. I am left with semi-direct, direct solenoids or changing to a motorized ball valve.
Some extra details:
- No fast acting required
- Fluid is a solution of water and non corrosive liquid ink with no solid pigments, at a maximum temperature of 80C (about 172F)
- Pipe ID for the outlet of the gravity fed 2/2 valve is 10mm (4 inches), but for the 3/2 valve it is still undefined. I can only assume that if I get a 20mm bore valve feeding into a 10mm ID pipe, it would be overkill. Correct me if I am wrong!
So, my questions are:
1. Would a semi-direct valve work better than a direct? Are you 100% positive it would work with such low dP?
2. Would a hollow ball valve induce less pressure drop? I am using the WMachine pump (with the inneficient rectangular paddle-like impeller) which already struggles to maintain a decent flow of water for the purpose since I had to route the outlet a bit higher and these pumps aren't really known for having a high head. Solenoid valve internals typically have a higher pressure drop.
If there's something I am unaware of, please, feel absolutely free to point it out! Oh, and sorry for the long post!
Have a great day.
Cheers,
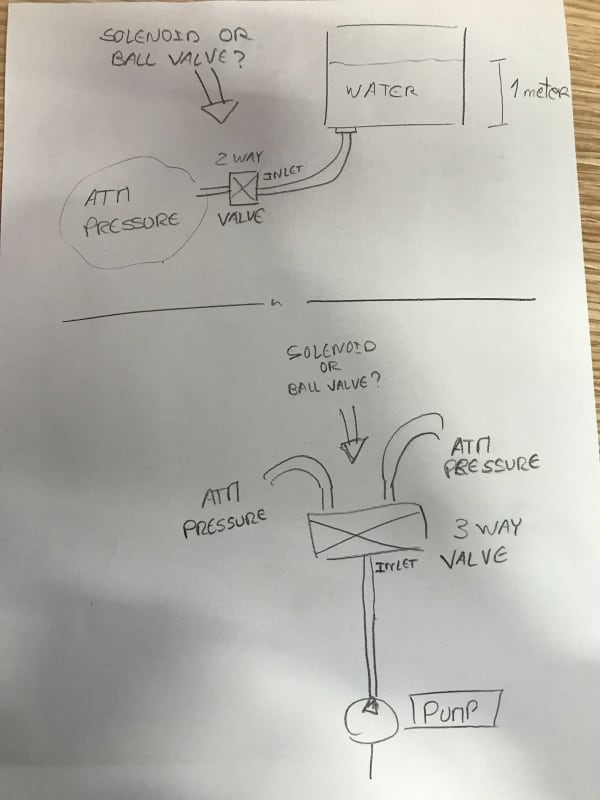
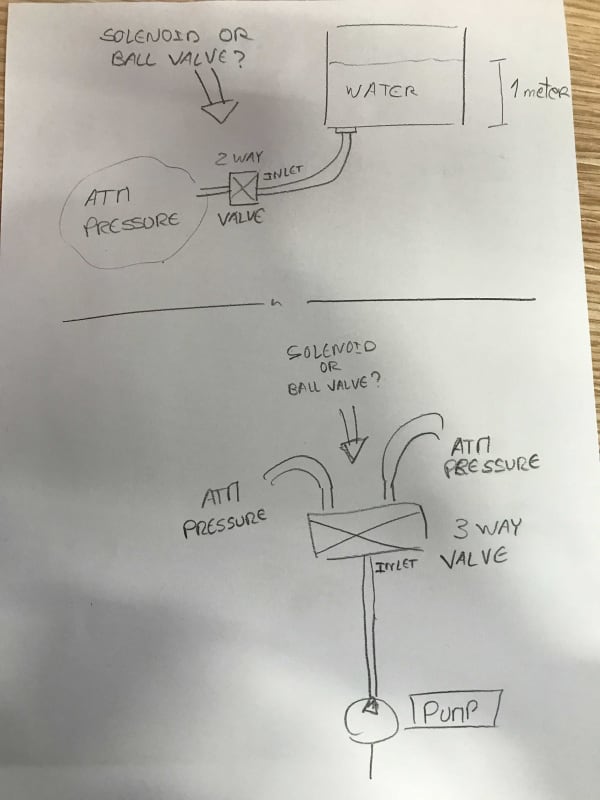
Adriano Pires.