Hi everyone,
I'd like to get some input on this project I am working on. The client owns an A-frame cabin that was built in the 1960s in an extremely high snow load area (around 250 psf ground snow load). The A-frame is constructed with 3x10 beams spaced at 48" o.c. with 2x6 T&G running perpendicular to the beams. This last winter the client noticed that one of the beams had an approximately 3" deep vertical crack. As the snow melted away he noticed that the crack closed. Where the crack ends there is also a horizontal crack along the length of the beam that is around 40" long. The owner is asking us to provide a repair for the beam that doesn't involve replacing it altogether. I have attached a picture of the beam in question along with a proposed repair that I am working on. It is a work in progress, but my idea is to provide a 1/4" steel plate on each side of the beam and bolt through.
Before I get too deep into this I wanted to see what your opinions would be about recommending this fix to the owner. I haven't nailed down how long the plate would be and how many bolts I'd recommend, but do you think this general idea would be a good repair for the beam? Outside of this I can't think of any other reasonable fix for the beam. I appreciate any feedback you have. Thanks!
I'd like to get some input on this project I am working on. The client owns an A-frame cabin that was built in the 1960s in an extremely high snow load area (around 250 psf ground snow load). The A-frame is constructed with 3x10 beams spaced at 48" o.c. with 2x6 T&G running perpendicular to the beams. This last winter the client noticed that one of the beams had an approximately 3" deep vertical crack. As the snow melted away he noticed that the crack closed. Where the crack ends there is also a horizontal crack along the length of the beam that is around 40" long. The owner is asking us to provide a repair for the beam that doesn't involve replacing it altogether. I have attached a picture of the beam in question along with a proposed repair that I am working on. It is a work in progress, but my idea is to provide a 1/4" steel plate on each side of the beam and bolt through.
Before I get too deep into this I wanted to see what your opinions would be about recommending this fix to the owner. I haven't nailed down how long the plate would be and how many bolts I'd recommend, but do you think this general idea would be a good repair for the beam? Outside of this I can't think of any other reasonable fix for the beam. I appreciate any feedback you have. Thanks!
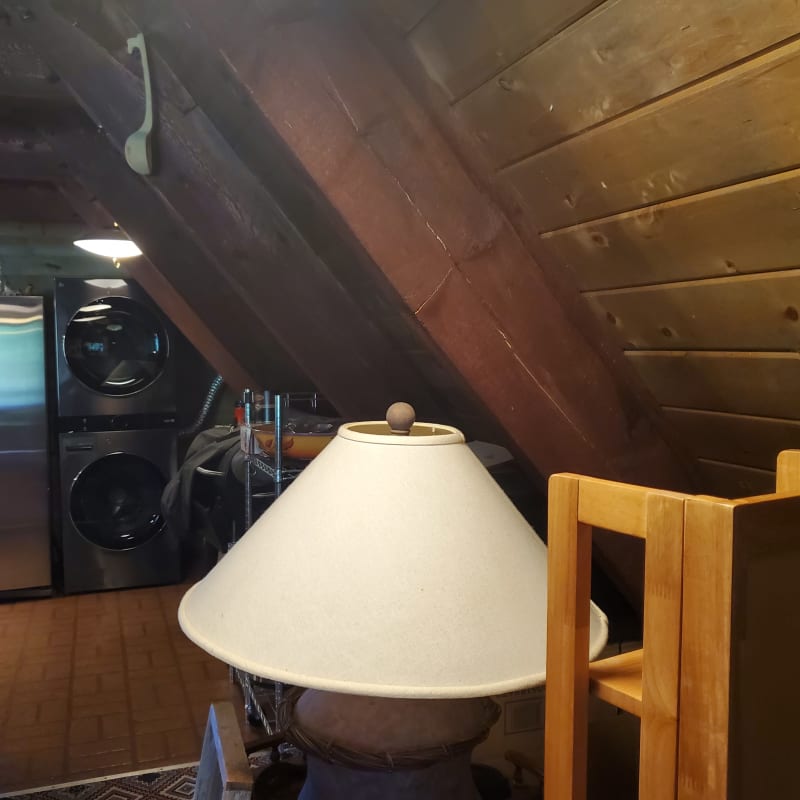
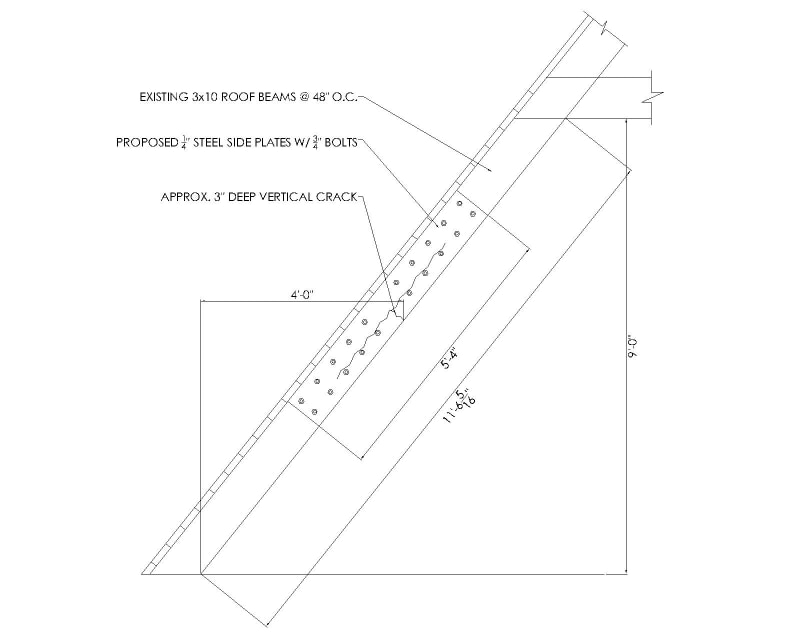