Ben29
Structural
- Aug 7, 2014
- 325
I have a tiny house that is getting a huge vertical addition. The existing exterior walls are comprised of 2x4 studs at 16"o/c. The owner wants to keep the existing roof framing and wall framing in tact. Note in the drawings below how they want to add a tiny knee wall on top of the existing 2x4 stud wall, and then add a new floor and 2x6 stud bearing wall above. Of course I will check to see if the existing wall works for the additional load, but furthermore I am concerned about this "kneewall situation" - should I be?
Also, is there anything that I need to be careful of when installing a new 2x6 stud bearing wall above an existing 2x4 stud bearing wall? I read online that this is a common practice for renovations, but I personally have never done that before.
PS: KootK, if you are reading this, congrats on being engineer of the week!
Also, is there anything that I need to be careful of when installing a new 2x6 stud bearing wall above an existing 2x4 stud bearing wall? I read online that this is a common practice for renovations, but I personally have never done that before.
PS: KootK, if you are reading this, congrats on being engineer of the week!
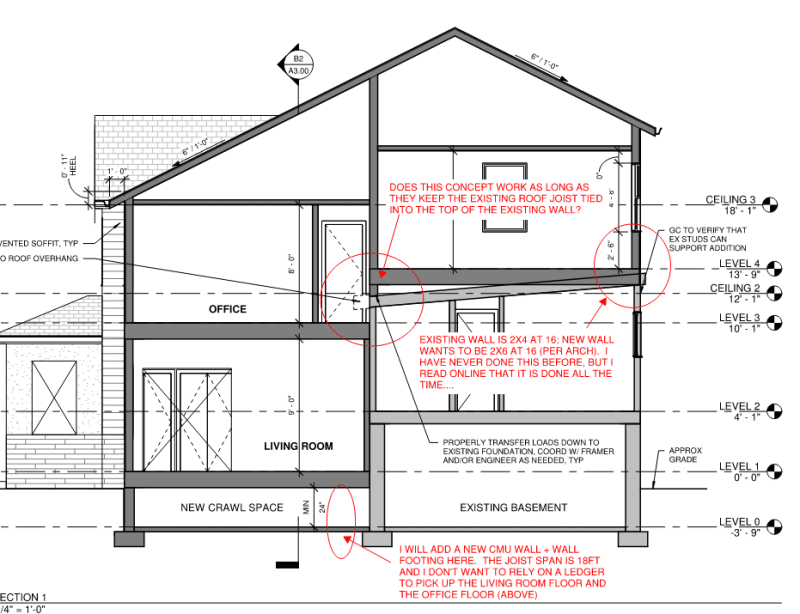