I have come accross an item (a spiral bevel gear set), which has been reportedly made of 17NiCrMo6 (1.6566) carburizing steel and the surface hardness is 68 HRc, while a typical would be around 58-62 HRc. Does anybody know how did they achieve 68 HRc on this steel?
Here's more information:
The items were checked with two different Rockwell Hardness Testers and the result was always 68 HRc. Then the gears were sent out to a laboratory for a material analyzis. They have reported a microhardness HV 0.8N (80G) at distance from the surface .05-2.0 mm as follows:
The chemical composition:
The surface layer structure:
The surface layer:
Based on these results they have indentified the material as 17NiCrMo6 after carburizing. A 1 mm thickness of the layer with minimal hardness of 550HV has been reported and that the maximum hardness of 940 uHV equals to approx. 68 HRc.
Here's more information:
The items were checked with two different Rockwell Hardness Testers and the result was always 68 HRc. Then the gears were sent out to a laboratory for a material analyzis. They have reported a microhardness HV 0.8N (80G) at distance from the surface .05-2.0 mm as follows:
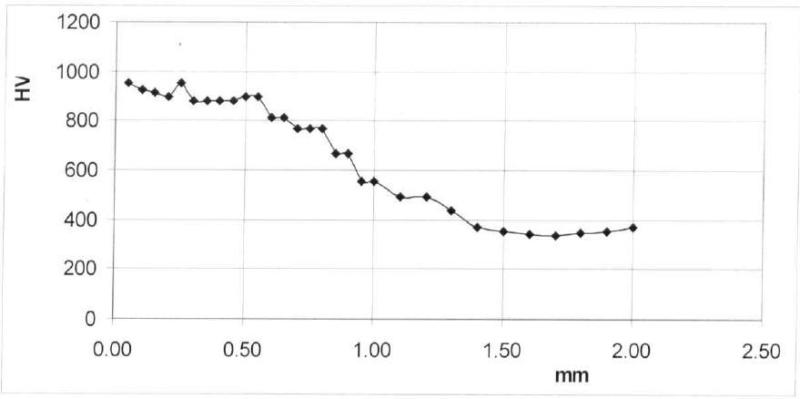
The chemical composition:

The surface layer structure:
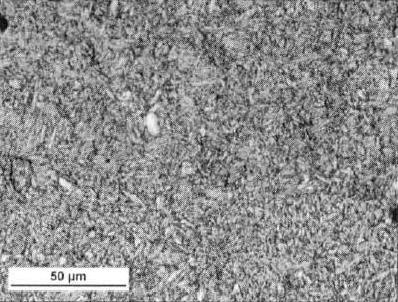
The surface layer:
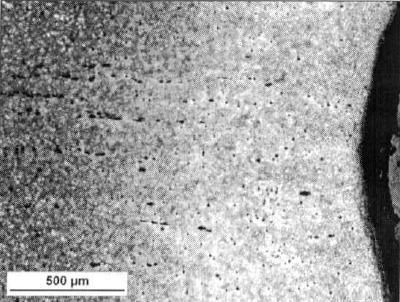
Based on these results they have indentified the material as 17NiCrMo6 after carburizing. A 1 mm thickness of the layer with minimal hardness of 550HV has been reported and that the maximum hardness of 940 uHV equals to approx. 68 HRc.