vivekigles
Industrial
- Aug 1, 2022
- 4
Please Support !!!!
We are using a vibration welding machine manufactured by Branson (A division of Emerson) & we are facing the issue of burr on regular basis. To reduce the burrs we have tried to reduce the amplitude of the machine by 0.03mm but it did not help. I have attached some pictures of parts with burrs and Welding parameters set value vs result value.
We are using the process for Welding two plastic parts. (The surface where the weld is to be made is linear and smooth).
Please suggest what else we can try to resolve this issue.
We are using a vibration welding machine manufactured by Branson (A division of Emerson) & we are facing the issue of burr on regular basis. To reduce the burrs we have tried to reduce the amplitude of the machine by 0.03mm but it did not help. I have attached some pictures of parts with burrs and Welding parameters set value vs result value.
We are using the process for Welding two plastic parts. (The surface where the weld is to be made is linear and smooth).
Please suggest what else we can try to resolve this issue.
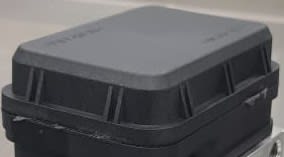
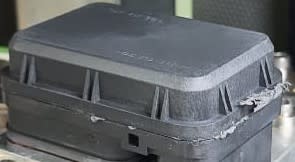
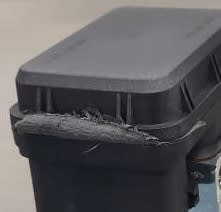
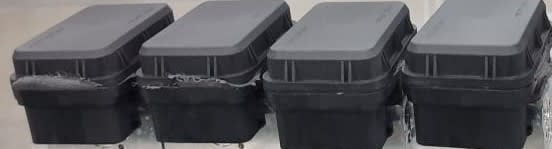
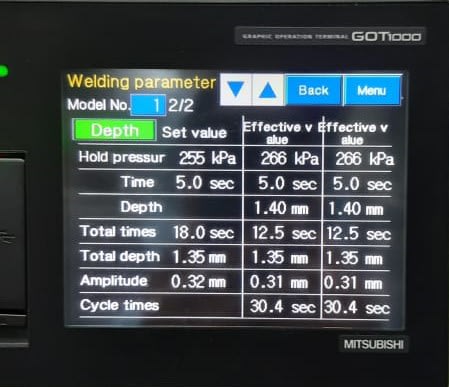
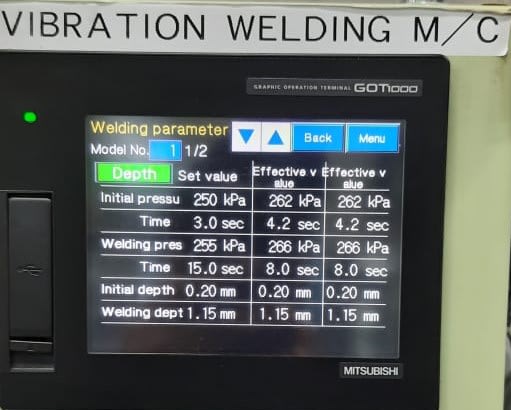