Jack Benson
Industrial
In our system we have a small diaphragm pump that vibrates when in use.
We use swivel fittings in our system, and the manufacturing process i have taken over involves adding a drop of glue to every join as the previous system designer thought it would stop vibrations loosening the joins
This video is from the production line.
I want to remove the glue as it makes servicing the device much harder as disassembly is much harder as the glue is strong.
Also, if there are mistakes in the production process and joins are not connected properly cannot be easily fixed with a simple tightening.
How can i find best practice for systems that have to maintain water tightness where there are vibrations?
thank-you
We use swivel fittings in our system, and the manufacturing process i have taken over involves adding a drop of glue to every join as the previous system designer thought it would stop vibrations loosening the joins
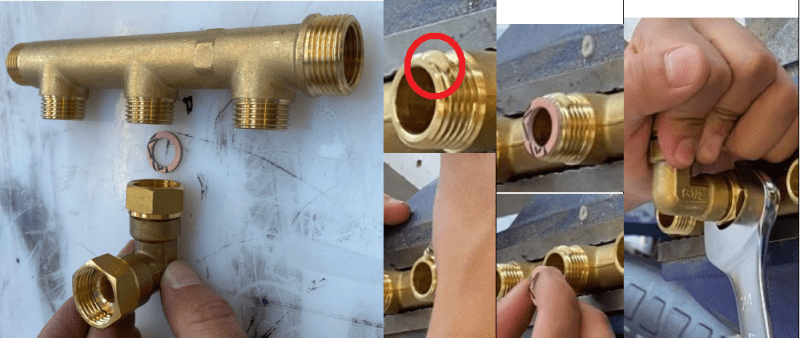
This video is from the production line.
I want to remove the glue as it makes servicing the device much harder as disassembly is much harder as the glue is strong.
Also, if there are mistakes in the production process and joins are not connected properly cannot be easily fixed with a simple tightening.
How can i find best practice for systems that have to maintain water tightness where there are vibrations?
thank-you