We have two stage RO plant of capacity 75 m3/h (permeate)[/color] and two high pressure pumps(51 m3/h each) are installed to maintain the feed flow. The raw water flowrate is 94 m3/hr . The throttle valve flow control strategy is applied along with the bypass. The whole scenario is shown in attached picture.
Note : Membranes type is CPA3 Hydranautics
High pressure pumps are vertical multistage centrifugal pump with 37 KW rated capacity motor.
Some of the parameters are as follows:
1- Inlet pressure of the High pressure pumps is 2 bar
2- Outlet pressure of the High pressure pumps when both are running in parallel is 20 bar
3- Pressure after throttle valve is 15 bar which means requirement of the membranes is 15 bar
4- Pressure drop after first stage of RO is 12 bar
5- Booster pump boost the pressure to 15 bar again for 2nd stage RO.
I have some questions related to it and would appreciate the reply from experts.
1- What throttle valve actually do? Does it control pressure or flow?
2- As mentioned above the pressure requirement for the membrane is 15 Bar but the pumps are generating 20 bars. Why do we need pumps or higher pressure and flow?
3- Would it be feasible/worth it to install VFD on one pump and other pump will work on fixed speed.
4- Do you think pump are sized properly?
Note : Membranes type is CPA3 Hydranautics
High pressure pumps are vertical multistage centrifugal pump with 37 KW rated capacity motor.
Some of the parameters are as follows:
1- Inlet pressure of the High pressure pumps is 2 bar
2- Outlet pressure of the High pressure pumps when both are running in parallel is 20 bar
3- Pressure after throttle valve is 15 bar which means requirement of the membranes is 15 bar
4- Pressure drop after first stage of RO is 12 bar
5- Booster pump boost the pressure to 15 bar again for 2nd stage RO.
I have some questions related to it and would appreciate the reply from experts.
1- What throttle valve actually do? Does it control pressure or flow?
2- As mentioned above the pressure requirement for the membrane is 15 Bar but the pumps are generating 20 bars. Why do we need pumps or higher pressure and flow?
3- Would it be feasible/worth it to install VFD on one pump and other pump will work on fixed speed.
4- Do you think pump are sized properly?
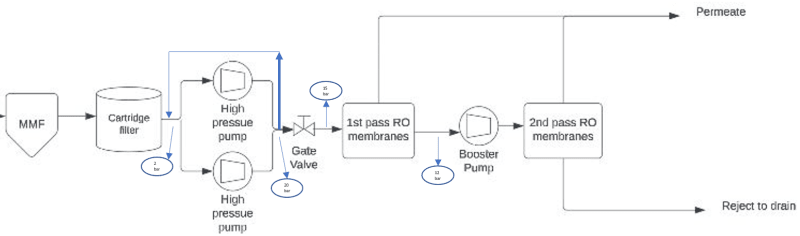