Kakashi-01
Chemical
I am currently working on an energy management project focused on an industrial warehouse (pulp). I am trying to understand how the warehouse is heated to estimate the energy used and suggest energy saving measures. From what I understand so far, glycol is heated either by a separate boiler (its operated only in winter) using natural gas or by steam from another boiler. The steam exits the boiler header and splits to serve multiple purposes: production processes, electricity generation, and heating glycol (desuperheating steam).
The hot glycol flows through pipes and splits off to unit heaters, where fans move air across the glycol coils to heat the surrounding air in the warehouse. Additionally, the glycol heats air in air handling units, which recirculate the air, and it also heats air from the makeup air unit.
For controlling warehouse temperature, they rely on an On/Off fan operation with the following control logic:
When the fan switch is set to "AUTO," the fan operates only if the warehouse temperature drops below the set point (7°C).
When the fan switch is set to "ON," the fan runs continuously, regardless of the temperature.
I asked people in the facility they told me they have no other controlling method.
For airflow, I asked whether the building has vents to exhaust air. I was told there are no dedicated vents, so the makeup air from the main air handler simply finds its way out of the building naturally. The warehouse walls are concrete, and the door heaters, mounted above the doors, provide adjustable air curtains with 90° nozzles pointing downward to prevent cold air inflow.
My concern: With no dedicated vents and the present control method won’t the continuous heat addition from glycol lead to a gradual temperature increase in the warehouse?
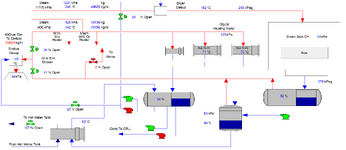
The hot glycol flows through pipes and splits off to unit heaters, where fans move air across the glycol coils to heat the surrounding air in the warehouse. Additionally, the glycol heats air in air handling units, which recirculate the air, and it also heats air from the makeup air unit.
For controlling warehouse temperature, they rely on an On/Off fan operation with the following control logic:
When the fan switch is set to "AUTO," the fan operates only if the warehouse temperature drops below the set point (7°C).
When the fan switch is set to "ON," the fan runs continuously, regardless of the temperature.
I asked people in the facility they told me they have no other controlling method.
For airflow, I asked whether the building has vents to exhaust air. I was told there are no dedicated vents, so the makeup air from the main air handler simply finds its way out of the building naturally. The warehouse walls are concrete, and the door heaters, mounted above the doors, provide adjustable air curtains with 90° nozzles pointing downward to prevent cold air inflow.
My concern: With no dedicated vents and the present control method won’t the continuous heat addition from glycol lead to a gradual temperature increase in the warehouse?
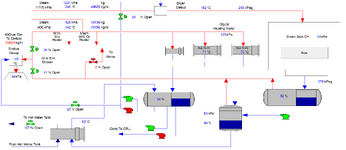
Attachments
Last edited: