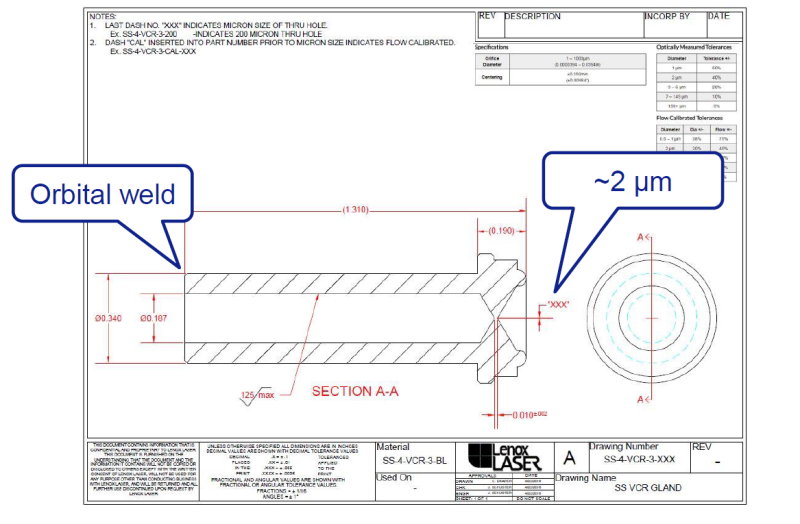
I am looking into orbital-welding the shown stainless-steel part to an ss tube and some couplings. However, some colleagues have expressed concerns that the welding process will warp the tiny, tiny 2 micrometer restriction hole at the end, possibly closing it or making it too large. I have a hard time believing that it will warp significantly (the tolerance on the hole diameter is already 20%), but I how do I convince them of this (if I am right)?
It seems that bending or stretching of the part should have minimal effect. Diametrical shrinkage or swelling would, at worst, have the same effect on the hole as on the whole part, so unless it's in the 10s percents, it won't be noticeable. Not to mention that the heat has a long way and a lot of material to go from the welding site to the restriction hole. We could also reduce the diameter of the tube at the welding site (it's outer diameter is too large anyway). Is there anything missing or incorrect from my logic?