Mr_Curious
Mechanical
- Jul 14, 2020
- 47
Hello everyone.
I am new at weld calculation. And I am looking for an information on how to calculate weld connections properly.
In particular, I have an electric motor with a terminal box that is welded on the side.
There are two welds, inside and outside of the box. I have tried to calculate it by Ansys, modelling the real weld shape and used mechanical properties of the electrode material but I don't really sure whether this is correct or not.
Could someone share information about how professionals design weld like this?
Thanks a lot in advance.
I am new at weld calculation. And I am looking for an information on how to calculate weld connections properly.
In particular, I have an electric motor with a terminal box that is welded on the side.
There are two welds, inside and outside of the box. I have tried to calculate it by Ansys, modelling the real weld shape and used mechanical properties of the electrode material but I don't really sure whether this is correct or not.
Could someone share information about how professionals design weld like this?
Thanks a lot in advance.
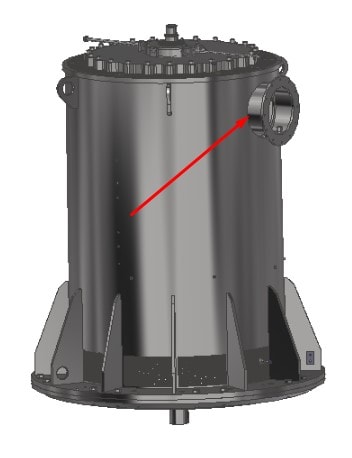
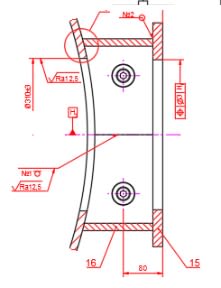
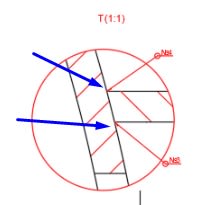