Hi,
In the bottom chord of a truss due to overstressed, it needs a plate reinforcement on the top side of the WT section for the force below in the image.
The new reinf. plate will be welded to the WT section for increased capacity. The tension force is 62 Kips from model. so while doing the weld length calculation.
1). Do we have to consider 62 kips and divide it bu the weld capacity of a particular size to get our weld length?
2). Do we have to consider 62+62 Kips as the tension force as its pulling apart in both ends, so sum up that force for both ends 124 Kips and divide by weld capacity to get our weld length
3). Since the weld direction is joined parallel to the direction of loading force can we ignore the weld design as per AISC Table J2.5 for fillet welds.
What is the realistic approach for the situation.
Thank you!
In the bottom chord of a truss due to overstressed, it needs a plate reinforcement on the top side of the WT section for the force below in the image.
The new reinf. plate will be welded to the WT section for increased capacity. The tension force is 62 Kips from model. so while doing the weld length calculation.
1). Do we have to consider 62 kips and divide it bu the weld capacity of a particular size to get our weld length?
2). Do we have to consider 62+62 Kips as the tension force as its pulling apart in both ends, so sum up that force for both ends 124 Kips and divide by weld capacity to get our weld length
3). Since the weld direction is joined parallel to the direction of loading force can we ignore the weld design as per AISC Table J2.5 for fillet welds.
What is the realistic approach for the situation.
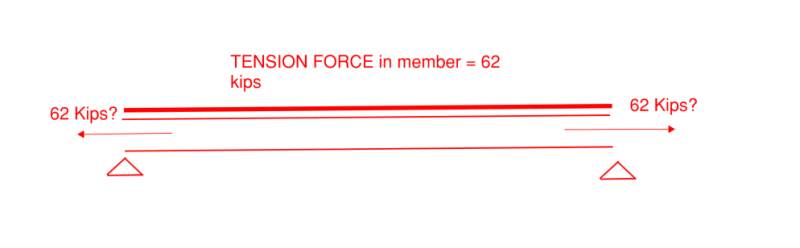
Thank you!