jbesson
Petroleum
- Feb 13, 2008
- 25
Dear Engineers,
In continuation to the thread794-422928 I would like your advice regarding the profile of flange face to be considered before WO (Weld Overlay) deposit.
In this configuration the WO deposit shall be 8.5mm after machining
-if we start with a standard flange the original groove shall be re-machined to allow 8.5mm WO deposit and the machining will reduce the flange thk which is not acceptable, so we have to increase the RF height
-if we start with a flat face flange we have to put enough WO to machine the groove + 8.5mm thk between bottom of groove and interface with flange base material -> ~25mm in this case
I consider that both options are acceptable, does anyone have experience/advise on this subject ?
Thanks in advance
In continuation to the thread794-422928 I would like your advice regarding the profile of flange face to be considered before WO (Weld Overlay) deposit.
In this configuration the WO deposit shall be 8.5mm after machining
-if we start with a standard flange the original groove shall be re-machined to allow 8.5mm WO deposit and the machining will reduce the flange thk which is not acceptable, so we have to increase the RF height
-if we start with a flat face flange we have to put enough WO to machine the groove + 8.5mm thk between bottom of groove and interface with flange base material -> ~25mm in this case
I consider that both options are acceptable, does anyone have experience/advise on this subject ?
Thanks in advance
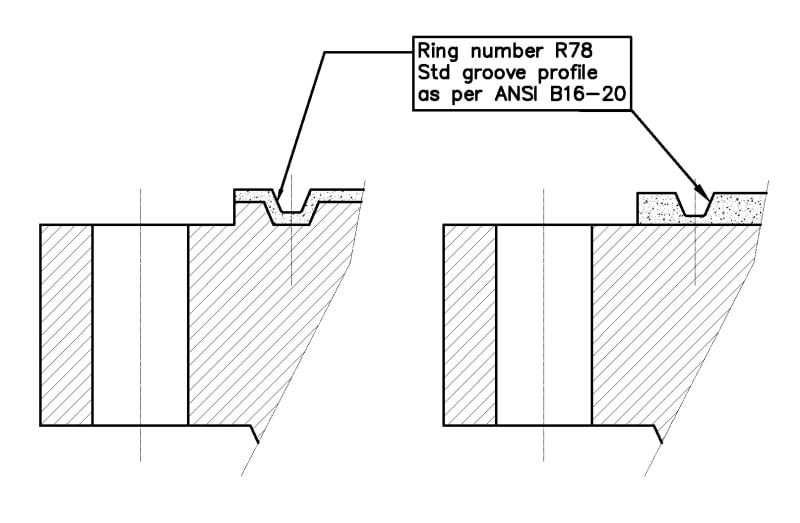